¿Cómo se fabrica realmente un neumático? Seguro que esta pregunta ha surgido en la cabeza de muchos alguna vez, sobre todo en los que no creen ese cierto bulo extendido de que los neumáticos se hacen simplemente colocando goma en un molde y cociéndola. Para alcanzar el gran nivel de calidad de los neumáticos actuales hace falta bastante más que eso.
Michelin nos invitó a su fábrica de Vitoria para ver in situ cómo son los procesos que desembocan en la creación de un neumático hecho y derecho. En esta factoría Michelin desarrolla neumáticos para turismos y para ingeniera civíl, es decir neumáticos especialmente creados para maquinaria de obras, camiones, etc. Precisamente ostentan el récord de haber creado la rueda de mayor tamaño, específicamente diseñada para un camión que puede pesar hasta 600 toneladas (como éste más o menos).
La visita consistió en un recorrido por todos las partes de la fábrica que forman el proceso de construcción de los neumáticos. Primero visitamos la zona en la que se tratan las materias primas que forman los neumáticos, como el caucho o el acero, para posteriormente pasar al proceso que comienza a estructurar los materiales que forman el neumático en el orden correcto.
Posteriormente accedimos a la zona en la que se le empieza a dar forma al neumático y por último pudimos ver en directo la coción del neumático, en la que gana la apariencia que todos conocemos. La construcción de un neumático es bastante más compleja que lo que se ha explicado hasta ahora así que para conocerlo en profundidad hay que estudiar a fondo lo que se hace en cada uno de los procesos.
Procesos de fabricación de un neumático
Hay tres procesos básicos en la fabricación de un neumático una vez se tienen las materias primas dispuestas: confección, conformación y cocción. Pero antes hace falta preparar y tratar los diferentes elementos que se utilizan en la fabricación. Se utiliza por supuesto caucho que puede ser sintético o natural. La proporción entre ambos cambia las propiedades de resistencia y de elasticidad.
También se utiliza el azufre que es un elemento clave en la cohesión del caucho cuando se realiza la cocción del neumático. En el proceso también interviene el negro de carbono, un producto que sirve como pigmento y como refuerzo de la goma, y el sílice. El acero es la materia utilizada para crear los hilos interiores del neumático, básicos en la adhesión de la llanta y el neumático.
Confección
La confección o el ensamblado sirve para comenzar a crear la base del neumático. Para ello se apilan en plano los distintos componentes del neumático sobre un tambor con el que empieza a tomar forma. Cada uno de los componentes debe ir en una posición específica y el orden de colocación de los mismos es vital para conseguir un buen resultado.
El primer componente que se imprime sobre el tambor para crear los neumáticos sin cámara es la goma interior. Ésta debe ser estanca al aire y al agua para que no existan filtraciones en el interior del neumático. A continuación se incorpora la lona de carcasa de forma transversal y a cada lado de la lona se colocan los aros metálicos que darán firmeza al neumático.
Los últimos productos que se añaden en la confección son diversas gomas de relleno o de refuerzo como la que protege los francos. En este punto del proceso están estructurados los materiales pero el neumático todavía no tiene forma.
Conformación
A partir de este proceso el neumático empieza a “moldearse” y el producto final se conoce como “neumático crudo”. En primer lugar los componentes pasan de la forma cilíndrica a la de anillo tórico, que ya se va pareciendo a la forma habitual de un neumático.
Para llevar a cabo esta acción se somete una presión de inflado a la zona central del neumático, con lo que se hinchan y se tensan las capas de goma. Los aros creados en la conversión se acercan entre sí. A continuación la lona del cinturón de la cima y la banda de rodamiento, que todavía no tiene los dibujos habituales, se enrollan sobre el anillo.
A estas alturas el neumático crudo todavía conserva unas propiedades elásticas que lo harían inútil de cara a usarse como un neumático de verdad. Debe pasar al proceso de cocción en el molde para adquirir las características necesarias para su uso.
Cocción
La última etapa de la fabricación del neumático pasa por la colocación del neumático crudo en un molde en el que será cocido. En el molde el agua circula por una membrana interior que se hincha y comienza a pegar el neumático a las paredes interior, donde se encuentran los dibujos y las marcas que llevará finalmente. Durante la cocción, que dura unos 10 minutos a 150º, se produce el proceso conocido como vulcanización.
La goma de deja de tener un carácter plástico y deformable para adquirir la resistencia, firmeza y elasticidad necesarias, aspectos que dependen del grado de vulcanización. La base química de esta transformación se basa en la adhesión del azufre a las moléculas de caucho para que éstas no puedan separarse. Una vez cocido el neumático se separa del molde y comienza a enfriarse, tomando la forma final. El enfriamiento se produce al aire libre.
Revisión de los neumáticos. Desarrollo con las marcas.
Una vez secado el neumático no pasa directamente a la venta sino que primero es revisado porque debe cumplir unos mínimos de calidad. Es decir, antes de llegar al consumidor hay que probar que la resistencia, la flexibilidad y la elasticidad son las buscadas inicialmente, que el dibujo esté correctamente impreso en la banda de rodadura, etc. Para ello hay dos tipos diferentes de controles, los manuales y los automáticos.
Los manuales consisten esencialmente en tocar el neumático, sentir si tiene esa consistencia necesaria, si tiene un buen aspecto o si los dibujos están bien hechos. Este proceso lo realizan personas especializadas en el tema sin complicados instrumentos. Las comprobaciones automáticas consisten en el análisis por ultrasonidos y por rayos X con los que se puede ver si las estructuras interiores están en buen estado. Si las pruebas dan al neumático como correcto, es decir que está dentro de unos márgenes de error predeterminados, pasa a ser apto para la comercialización.
En muchas ocasiones el fabricante de neumáticos y los fabricantes de coches entran en comunicación directa para desarrollar un modelo. El segundo le pide al primero unos neumáticos específicos para adaptarlos a un coche en concreto, en busca de un consumo o de una rumorosidad reducida. En ese caso se desarrollan distintos neumáticos de prueba, hilando fino la proporción de materiales o su colocación para alcanzar distintas características, y se fabrican rápidamente.
También en muchos casos nada más enfriarse el neumático creado se coloca en el coche y se realizan las pruebas. Según los resultados de los probadores se escoge el neumático o se vuelve a comenzar desde el principio. Para los fabricantes de coches el neumático es una parte muy esencial para poder homologar un determinado consumo por ejemplo, puesto que las gomas influyen notablemente en el gasto de carburante.
El siguiente vídeo explica de forma resumida y sencilla cómo se fabrica un neumático desde el principio hasta el final.
Fábrica de Michelin en Vitoria
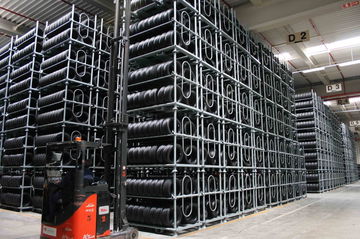
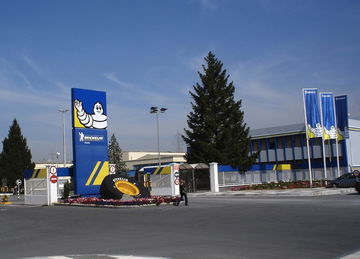
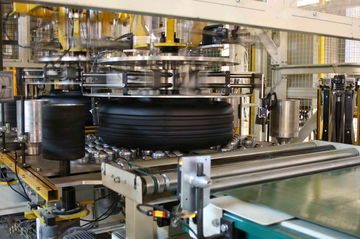
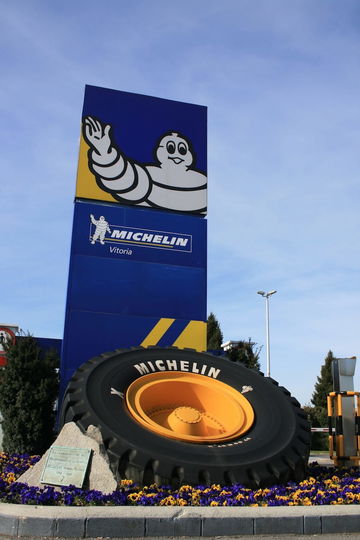

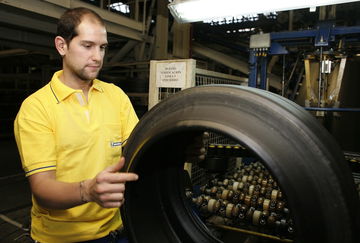
En Diariomotor: Cómo se hacen las pruebas de neumáticos en el TÜV | Prueba y presentación de los neumáticos Energy Saver de Michelin | El neumático: denominaciones, medidas y consejos de seguridad