El futuro de la industria del automóvil sigue girando en torno al acero. Hyundai cree firmemente en ello y por esa misma razón su estrategia para los próximos años, como su pasado, seguirá estando ligada a un material conocido por la humanidad desde hace más de veinte siglos. La apuesta de Hyundai por lo tanto pasa por seguir aprovechando las cualidades del acero, en su mayoría producido en casa por su filial Hyundai Steel, y la versatilidad de las últimas aleaciones de alta resistencia sin olvidarse de que la democratización del aluminio, la fibra de carbono y los plásticos reforzados, es cuestión de tiempo.
Antes de fabricar coches, Hyundai hacía acero, siendo la industria acerera más antigua de Corea y actualmente una de las diez más importantes del mundo por volumen. Con estos precedentes, Hyundai comenzó a fabricar barcos, inmensas construcciones, maquinaria pesada y por supuesto automóviles. Hoy en día las diferentes compañías del inmenso grupo Hyundai trabajan de manera independiente, lo que no resta méritos a que el 35% del acero empleado por Hyundai Motor Company (Hyundai y Kia), con más de 4,4 millones de coches producidos en 2012, provenga de Hyundai Steel y acerías como la del impresionante complejo de Damgjin que conocimos durante nuestra visita a Corea del Sur.
El acero ha sido el origen de Hyundai y en buena parte uno de los responsables del crecimiento de Corea del Sur desde que finalizase su guerra. En Seúl y alrededores apenas quedaban algo más de 2 millones de habitantes hace sesenta años, tras la Guerra de Corea. Actualmente en este reducido espacio de tierra viven más de 25 millones de personas, la mitad de la población total del país.
Creedme que para cualquiera que trabaje en la industria del automóvil o simplemente tenga curiosidad por la industria, en general, y cómo se fabrican los productos de una sociedad desarrollada, existen pocas oportunidades tan provechosas como conocer el proceso de construcción de un automóvil desde su materia prima, el mineral de hierro.
Hoy un servidor puede presumir de haber tocado con sus propias manos el mineral recién llegado de Brasil en la factoría de Damgjin antes de la hora de comer, ver como se fundía en los inmensos y recién estrenados hornos de Hyundai Steel, atender a su procesamiento por Hyundai HYSCO antes de llegar a las fábricas y más tarde ver como se prensaba ese acero para conformar un coche en la factoría de Asan y por supuesto ver como un operario accionaba el contacto en ese momento mágico que es el primer arranque de un coche a la hora que deberíamos estar tomándonos la merienda. En apenas unas horas habíamos asistido a un proceso largo y complejo, la magia por la cual la materia prima se había transformando en un flamante Sonata.
La razón por la cual estas fotografías nos las ha proporcionado directamente Hyundai, tal y como se aprecia en la marca de agua de la esquina inferior derecha, es que como en muchas otras zonas no se nos permitió el uso de cámaras fotográficas. Toda precaución es poca ante el riesgo de espionaje industrial.
Tras nuestra visita a la acería de Damgjin, nos desplazamos hasta Asan para conocer las líneas de producción en las que se ensamblan el Grandeur (Azera en Estados Unidos), el nuevo Sonata (YF y también el Hybrid) y el antiguo Sonata, que aún sigue fabricándose para servir de taxi en Corea del Sur. Esta fábrica atiende una producción anual de más de 300.000 unidades, aunque ninguna de ellas llega a este lado de Europa.
Lo mismo sucede con la inmensa factoría de Ulsan, la más grande de la industria del automóvil en todo el mundo. Hablamos de una producción anual de 1,5 millones de coches, una tercera parte de la producción total de Hyundai y Kia, 6.000 unidades diarias en un inmenso complejo que cuenta con su propio puerto. En lo tecnológico y en el desarrollo de los procesos de calidad de la factoría de Asan, no nos pareció que esta fábrica tuviera nada que desmereciera frente a otras que en los últimos años hemos visitado en Europa.
La automatización ha logrado que la productividad de Asan sea realmente alta. Hablamos de tres robots por operario en prensas de acero y una labor manual más intensa en líneas, como la de montaje de interiores, que aún siguen requiriendo la delicadeza del trabajo manual. También se ha logrado que el margen de error sea realmente pequeño, sobre todo si tenemos en cuenta que todas y cada una de las piezas que salen de la prensa pasan por un análisis milimétrico vía láser que decide si la pieza es correcta o requiere ser descartada o corregida.
Tal vez esté alardeando de mi ignorancia, pero nunca había visto una fábrica en la que algunas líneas tuvieran una banda sonora constante con una irritante cancioncilla típica de un organillo de juguete. Este es un ejemplo más de las peculiaridades de las culturas asiáticas. En vez de contar con un aviso, no menos irritante, sonoro cuando una línea está detenida por un fallo (algo realmente común), los operarios se percatan de tal eventualidad por la melodía que emiten las máquinas, si esta cambia indicará que la máquina ha fallado.
No obstante y para aquellos que valoren que en un automóvil se produzca en Europa, no nos podemos olvidar que el grueso de los automóviles que se comercializan por Hyundai en España han sido fabricados en República Checa y Turquía.
Creo firmemente en que Hyundai hace bien en seguir trabajando el acero y mejorando sus cualidades mediante el uso inteligente de aceros reforzados, de alta resistencia, para mejorar la rigidez estructural y la seguridad incluso reduciendo el grosor, y por ende el peso, de las láminas de acero utilizadas en la prensa. No se trata de una innovación de Hyundai, de hecho cada vez son más las marcas que potencian el uso de este tipo de aceros. Pero sí una medida que en muchos casos y junto a otras mejoras, como el empleo de motores más pequeños, puede conseguir que un modelo de nueva generación (incluso creciendo en cotas y equipando nuevas tecnologías) ahorre entre 50 y 100 kilogramos respecto a su predecesor.
Otra peculiaridad que os podemos contar acerca de la importancia de la estrecha colaboración entre Hyundai Steel y Hyundai Motor Company radica en que la primera cuenta con su propio centro de I+D para mejorar la calidad de los aceros fabricados y que las sinergias redunden en aceros que, si bien es cierto serán más caros, mejorarían el resultado final de los automóviles del Grupo Hyundai.
Y evidentemente con todo lo que ha invertido Hyundai en mejorar el acero, esta no es la única vía que seguirán en el futuro. De momento no se plantean comercializar automóviles que hagan uso extensivo de fibra de carbono, ni mucho menos, ni tampoco adaptar sus factorías con las autoclaves necesarias para fabricar piezas de cierto calibre con este material. Pero sí sabemos que en el centro de R&D de Hyundai ya se está investigando el uso de fibra de carbono para valorar su aplicación en un futuro quizás no tan lejano.
La producción de un automóvil, paso a paso, desde la materia prima
1. El mineral de hierro llega directamente en barcos y mediante unas inmensas grúas se traslada a unas cintas transportadoras que lo trasladan a su almacenamiento.
2. Hyundai Steel presume de contar con los mayores almacenes cerrados para el mineral de hierro de la industria acerera.
3. La fundición de acero circula por una línea completamente automatizada en la que se estira, toma consistencia y se enfría la inmensa placa de acero.
4. Las placas de acero se apilan y enrollan para su procesado en HYSCO.
5. HYSCO se encarga de procesar las placas de acero con diferentes grosores y tamaños para adaptarse a las necesidades de su cliente o de la factoría de Hyundai.
6. La materia prima de que se compone la mayor parte de la estructura de un coche, el acero, llega a la factoría de Hyundai en Asan en placas enrolladas que pesan entre 10 y 20 toneladas. Estas placas se desenrollan, se cortan y empiezan a tomar forma mediante las líneas de estampado, con un trabajo supervisado por operarios pero realizado única y exclusivamente por los robots.
7. Tras el estampado, las piezas de acero moldeadas pasan por una segunda comprobación milimétrica que se asegura de que el proceso anterior no ha fallado, en cuyo caso se procedería a su reparación o descarte.
8. Una vez se unen todas las piezas de acero y el esqueleto de la carrocería ha comenzado a tomar una forma que ya sí se asemeja un coche, la carrocería pasa por la línea de pintura y se aplica el color de la carrocería tras un proceso de imprimación y verificación.
9. Como muchas otras factorías, la de Asan no solo ensambla coches, también motores.
10. Para un neófito resulta verdaderamente sorprendente ver una fábrica a pleno rendimiento sin apenas operarios, las máquinas y los robots se encargan de prácticamente todo el proceso, salvo la etapa final de montaje del motor y ajuste de los revestimientos interiores, que es eminentemente manual.
11. Tras todo el proceso llega el momento mágico del primer arranque. Una fila de flamantes Sonata y Grandeur espera a que un operario accione el contacto y arranque por primera vez el motor. En este paso final la mayoría de los motores arrancarán y pasarán a una última etapa, aquellos que no lo hagan seguirán en la fábrica para solventar la incidencia y hacer los ajustes que sean necesarios y que impidieron ese primer arranque.
12. La última etapa en la factoría de Hyundai en Asan, una vez el coche ha arrancado correctamente, pasa por una pequeña pista de pruebas en las que los técnicos examinan que el automóvil funciona correctamente. Si hubiera algún problema lo solucionarían, y si no, el coche ya estaría listo para su transporte hasta el cliente final.
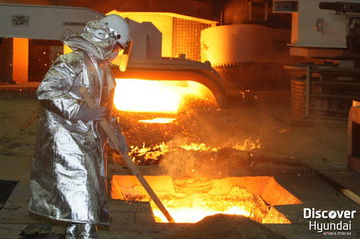
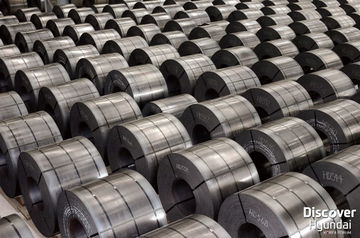
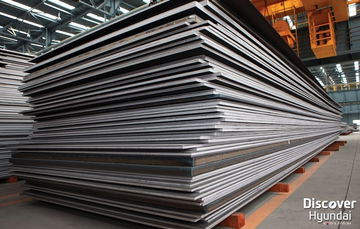
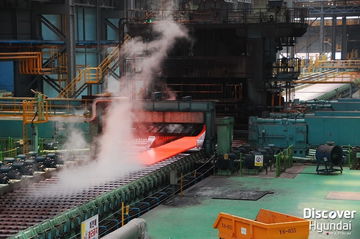
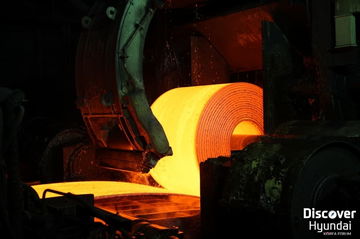
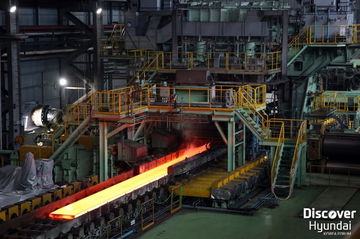