Hace unos días os hablábamos de un tema que nos preocupaba, y personalmente nos decepcionaba, el sobrepeso de los coches modernos. Ya os decíamos que se trataba de un mal necesario, si queríamos coches más seguros, bien equipados, y con un precio al alcance de todos los públicos, no había más remedio que ese para lograr estos objetivos. Lo interesante, y el golpe de optimismo que hoy podemos transmitiros, está precisamente en el hecho de que esa tendencia esté revirtiéndose. Por fin estamos comenzando a acostumbrarnos a que prácticamente cada coche que se presenta sea más ligero que su predecesor. Y hemos llegado a un punto en el cual ya podemos afirmar que muy pronto los coches serán más ligeros que nunca. Llevándonos hacia una filosofía, la de restar kilogramos, y necesitar menos potencia para cubrir con nuestras necesidades, que nos encanta.
Las mismas técnicas que han ayudado a mejorar la seguridad de nuestros coches, están consiguiendo que estos sean cada vez más ligeros. La pequeña revolución que hemos vivido en los últimos años en la industria del automóvil ha llegado de la mano de las aleaciones. Más allá de técnicas como el downsizing, reducir el tamaño de los motores para obtener la misma potencia, y prestaciones, mediante técnicas como la turboalimentación, los materiales están siendo una de las grandes claves del aligeramiento de nuestros coches.
Los fabricantes trabajan ya con nuevas aleaciones de acero que mediante diferentes composiciones de carbono y hierro, y diferentes procesos de fraguado, consiguen que una lámina de acero más fina y ligera goce de la misma resistencia que las láminas utilizadas hasta la fecha. Son los denominados aceros de alta y ultra-alta resistencia, materiales que sin elevar sobremanera el coste de producir un automóvil, pueden contribuir a adelgazar la masa de un coche moderno.
Los aceros de alta resistencia son solo el principio. El aluminio se está convirtiendo en uno de los materiales más habituales en las estructuras y la carrocería de los coches modernos. Trabajar con el aluminio, y con aleaciones más resistentes, y económicas de producir, está consiguiendo que muchos fabricantes puedan permitirse utilizar cada vez más este material. Más allá de los premium, de modelos como el Audi A4, que ya emplean aluminio en suspensiones, y paneles exteriores, como el portón del maletero, tenemos casos tan interesantes como el del Ford F-150. La nueva pick-up de Ford ha conseguido reducir su masa en más de 300 kilogramos gracias a un uso muy extenso del aluminio. Recordemos que estamos hablando de un auténtico best-seller del óvalo azul, que el año pasado vendió un total de 780.354 unidades en Estados Unidos.
Muy pronto nos acostumbraremos a que cada vez más coches, también generalistas, utilicen aluminio en más componentes estructurales y revestimientos exteriores. Esa fue precisamente una de las razones por las que el antiguo Audi A2, que recientemente cumplía diez años, sigue siendo para nosotros un coche de culto, un incomprendido que sin duda fue un adelantado a su tiempo.
En cualquier caso, tampoco hemos de olvidarnos de que el uso de nuevos materiales, además de requerir nuevas técnicas de producción, exige cierta adaptación para emplear nuevas técnicas de mantenimiento y reparación. Trabajar con el aluminio no es equiparable a trabajar con el acero. Y si hablamos de materiales aún más exóticos, la complejidad técnica aumenta aún más.
El aluminio es solo el principio. Ya estamos viendo como muchos fabricantes estudian el uso de otro tipo de materiales, como el titanio o el magnesio. El problema sigue estando en asumir ciertos retos, más allá del coste y la complejidad de su producción, o la disponibilidad de la materia prima. Hace un tiempo probamos un prototipo de Renault en el que se había recurrido al magnesio, más ligero, más resistente, y muy apropiado para crear piezas estructurales de gran tamaño. Imaginaos que el techo de un compacto ensamblado en magnesio podría pesar solo 4 kilogramos. Increíble.
Uno de los grandes problemas que Renault había encontrado a la hora de estudiar su uso en este prototipo, y en futuros modelos de producción, estaba precisamente en conseguir un proceso de soldadura apropiado para emplear elementos de magnesio junto al acero y el aluminio. Su tratamiento para garantizar su durabilidad, y su resistencia al paso del tiempo y a los procesos de pintura, también exigía el empleo de ciertas tecnologías que se están desarrollando en estos momentos. Renault aseguraba que, a medio o largo plazo, podrían hacer que el uso del magnesio fuera viable en próximas generaciones de Mégane, o incluso Clio.
La fibra de carbono también se plantea como una solución a medio plazo para conseguir este objetivo. Ya nos hemos acostumbrado a que ciertos deportivos, no necesariamente tan exóticos y caros como un superdeportivo de 600 CV, recurran a un uso masivo de la fibra de carbono. El mejor ejemplo lo tenemos en el Alfa 4C, y su monocasco de fibra de carbono. Y llegados a este punto nos vamos percatando de cuáles son los grandes problemas que impiden que la fibra de carbono sea un estándar, al menos en turismos generalistas, el coste y la complejidad de su producción. Elaborar piezas tan grandes como el monocasco del Alfa 4C exige el empleo de un instrumental muy concreto, y es muy costoso. Y esa es la razón por la cual su producción anual está muy limitada.
En cualquier caso, la fibra de carbono sí está comenzando a ganar terreno en su empleo en elementos más pequeños y manejables. Nos ha parecido especialmente interesante el caso del nuevo BMW Serie 7, en el que BMW ha creado lo que ellos denominan como Carbon Core. Esencialmente se basaría en una combinación inteligente de fibra de carbono, aluminio y acero. Para explicarlo de forma sencilla, e incluso vulgar, imagina que tienes una pajita con la que tomas un refresco, de plástico, que con poco esfuerzo se dobla, y que en su interior introduces una varilla de acero, gracias a la cual evidentemente no se doblará con tanta facilidad. BMW habría dado forma a esa idea creando estructuras de acero y aluminio en cuyo interior existe un núcleo de fibra de carbono.
Y esto es solo el principio. El futuro de la industria del automóvil se dibuja en torno al uso de materiales cada vez más ligeros y resistentes. Los compromisos de cara al futuro, principalmente los relacionados con las emisiones de gases contaminantes y eficiencia energética, exigen coches más ligeros. Esa necesidad es incluso mayor en torno a la llegada del coche eléctrico, que como consecuencia de los requisitos de sistemas de almacenamiento energético especialmente pesados, requieren de un mayor aligeramiento para obtener más autonomía, recorrer más kilómetros con una sola recarga.
De manera que los materiales, junto con otras técnicas, como el downsizing, consiguen que hoy en día podamos afirmar que, sin lugar a dudas, muy pronto gozaremos de coches más ligeros que nunca. Y eso es una noticia que, como mínimo, nos debe generar optimismo.
En Diariomotor:
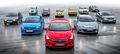