Así se fabrica en Molsheim uno de los deportivos más caros del mundo, el Bugatti Chiron.
2,4 millones de euros. 1.500 CV de potencia. Y un deportivo de altos vuelos tan impresionante como su proceso de fabricación. Ayer ya os contábamos 10 curiosidades acerca del Bugatti Chiron, su compra y su fabricación. Y ahora queríamos ir más allá para mostraros con más detalle cómo se fabrica un Bugatti Chiron en 24 fotografías de su factoría, un recinto con un suelo acrílico e impoluto, en el que no verás una mota de polvo, o una mancha de aceite, que desde la propia marca prefieren llamarlo como el Bugatti Atelier. Un Bugatti Chiron que se produce en un entorno aséptico, en el que no verás ni un robot, ni un proceso automatizado. Un entorno en el que la artesanía sigue estando presente, pese a la avanzada tecnología de la última obra de arte de Bugatti.
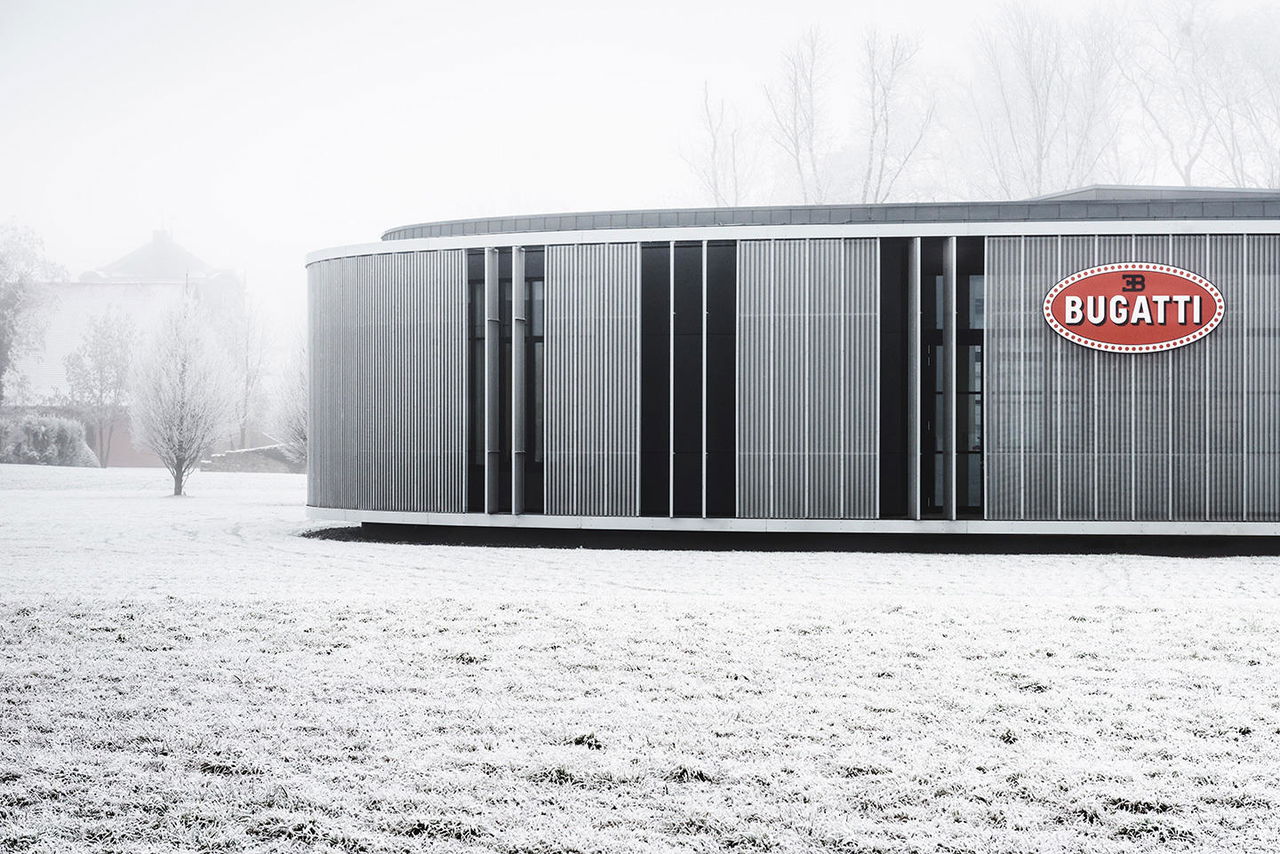
Bugatti Atelier. Como sucediera con su predecesor, el Bugatti Veyron, el Chiron sigue fabricándose en Molsheim, Francia. Al no tratarse de una fábrica al uso, Bugatti prefiere llamar a su factoría el Atelier, del francés taller. Para acoger la producción del nuevo Chiron, e introducir nuevos procesos, Bugatti tuvo que revisar por completo su Atelier, que cuenta con una superficie de 1.000 metros cuadrados.
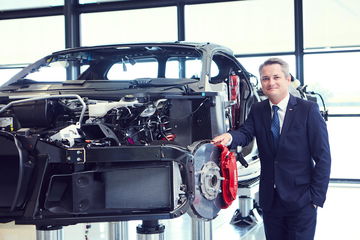
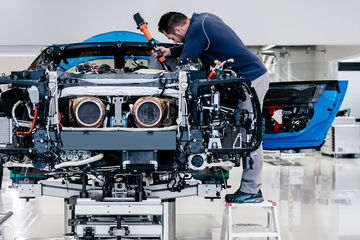
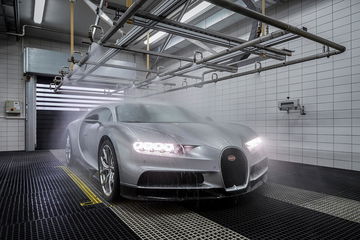
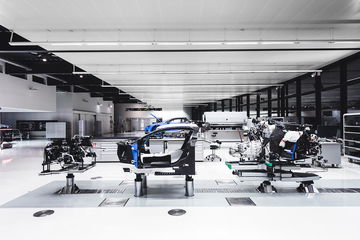
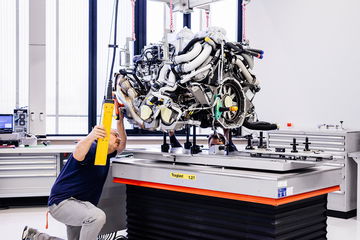
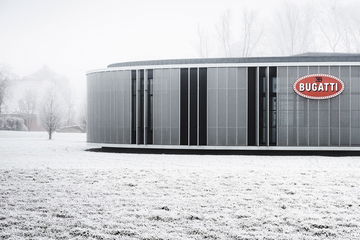
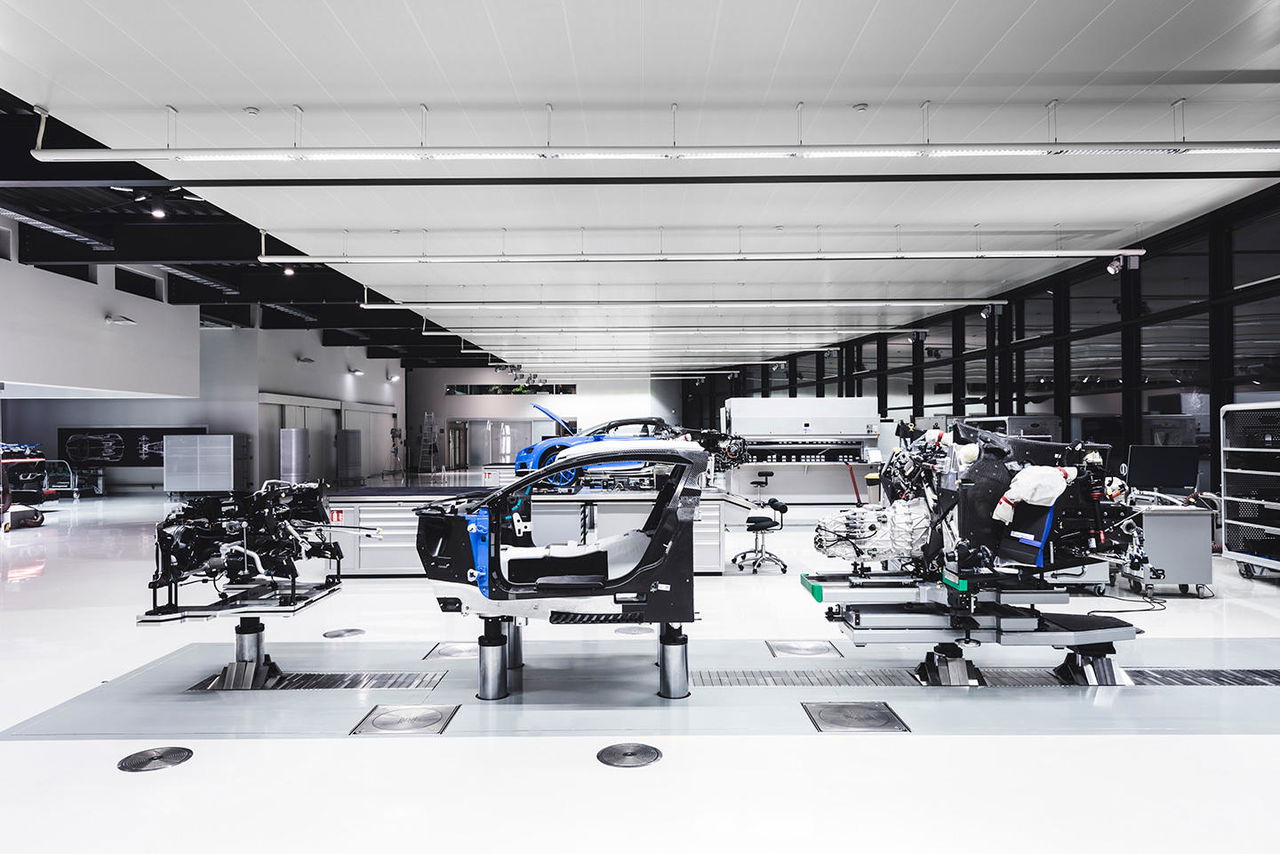
La personalizaciónEl proceso de ensamblado de un Bugatti Chiron comienza en el momento en que el cliente configura su deportivo, reuniéndose con el propio diseñador de Bugatti. Cuando está cerrada una configuración, Bugatti comienza a solicitar suministros de sus proveedores y a trabajar en el chasis.

El corazón del Bugatti Chiron. Los motores de dieciséis cilindros en uve doble y 1.500 CV de potencia del Bugatti Chiron llegan ensamblados desde la fábrica de Volkswagen en Salzgitter. Una de las primeras etapas del proceso de ensamblado de un Chiron comienza con su acondicionamiento. Cada motor pesa nada más y nada menos que 628 kilogramos. Pese al incremento de potencia, el motor del Chiron pesa exactamente lo mismo que el de su predecesor, el Veyron.
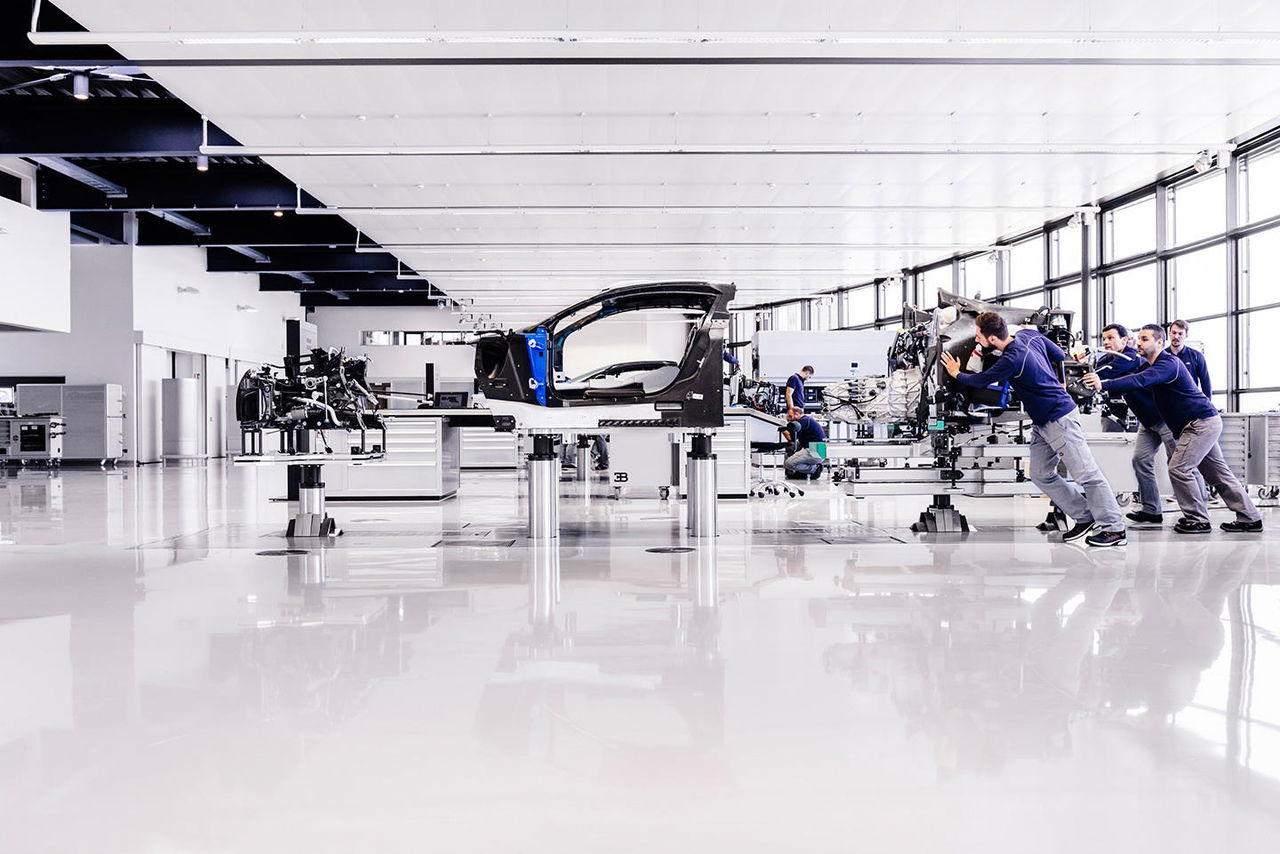
El matrimonio. El Bugatti Chiron se compone esencialmente de dos enormes piezas, su monocasco, y la sección posterior sobre la que reposa el motor. Estas dos piezas están conectadas únicamente por 14 tornillos de titanio, cada uno de los cuales pesa solo 34 gramos.
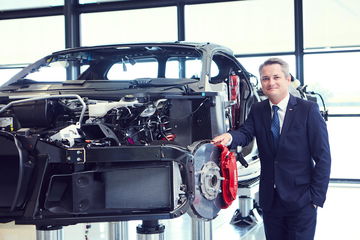
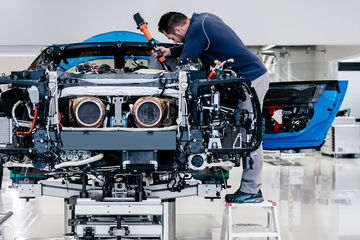
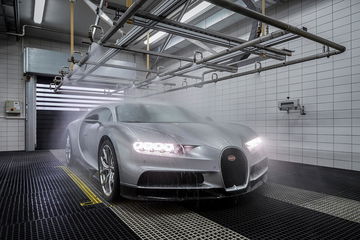
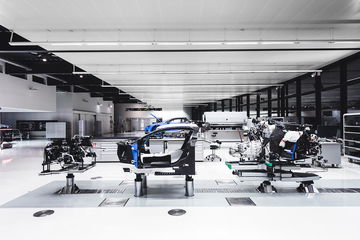
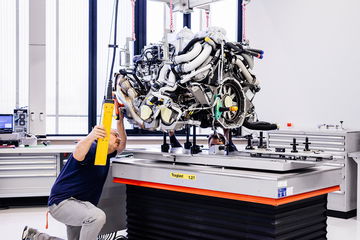
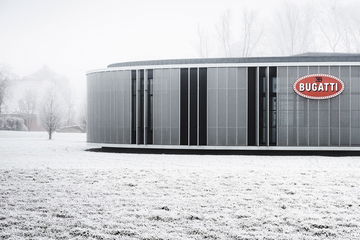
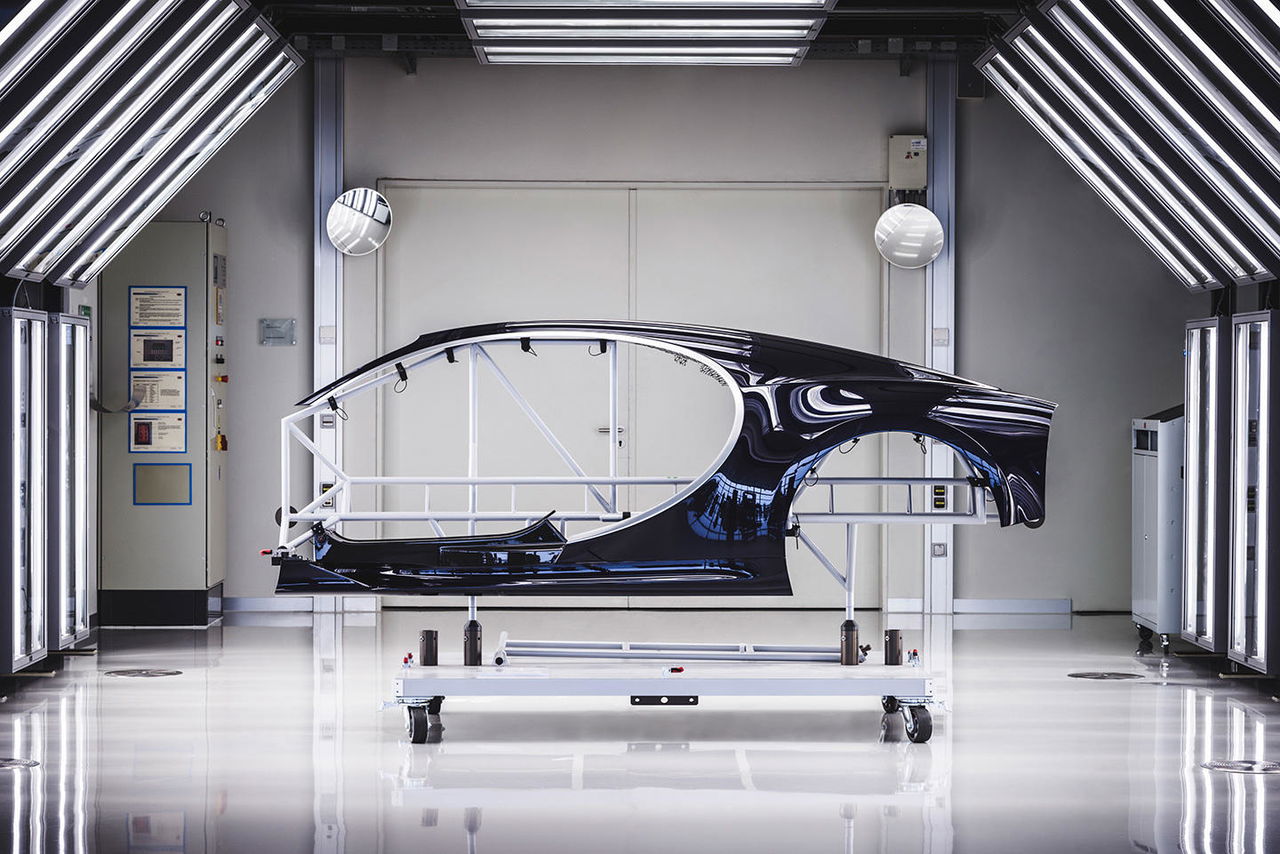
El monocasco. Antes incluso de que comience el ensamblado propiamente dicho, y desde que el cliente formaliza su reserva y configura su Bugatti Chiron, los operarios comienzan a trabajar en el monocasco y en su proceso de pintura, que se dilata durante tres semanas.
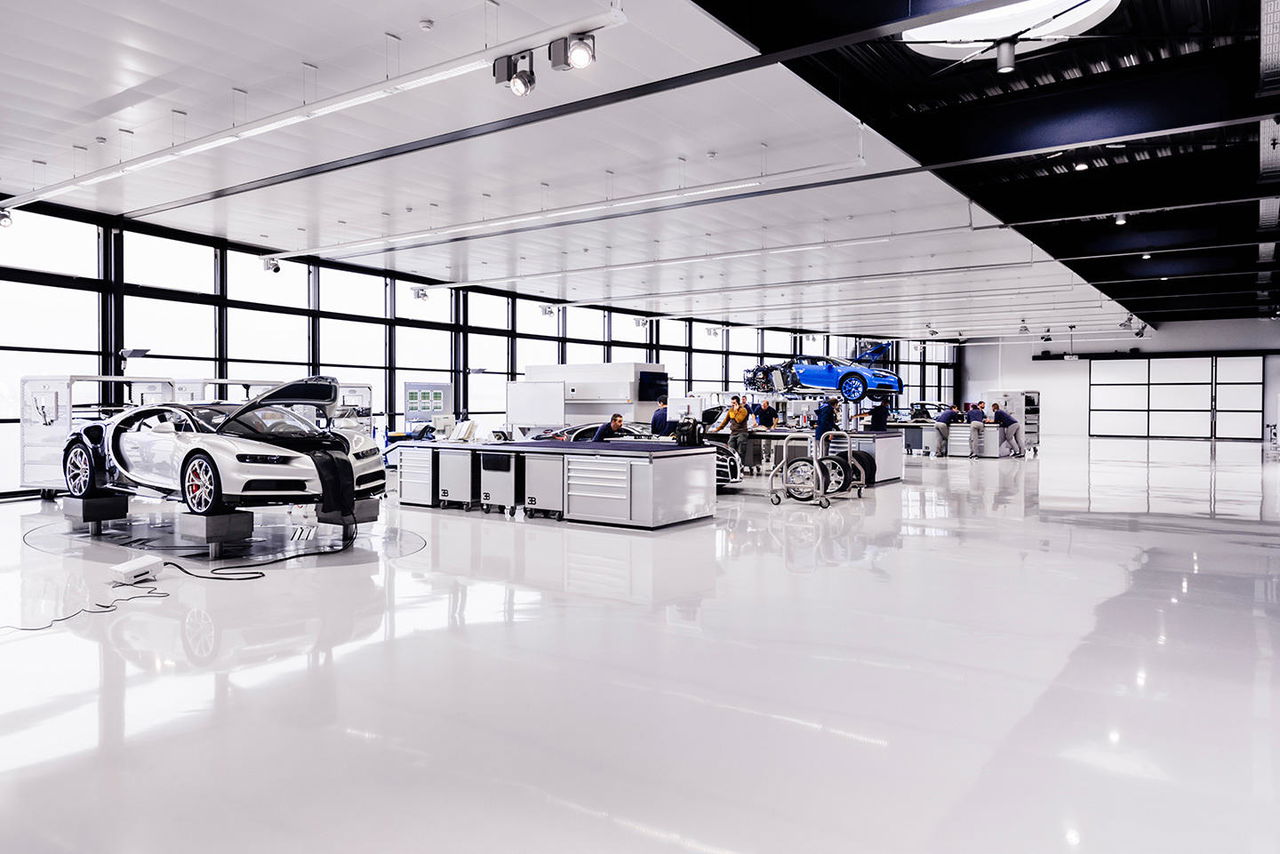
Artesanía. El proceso de ensamblado de un Bugatti Chiron es totalmente artesanal. Las líneas de la fábrica de Bugatti son más parecidas al taller de un equipo de Fórmula 1 que a una fábrica de turismos. No hay robots, ni líneas automatizadas, sino 12 estaciones de trabajo independientes.
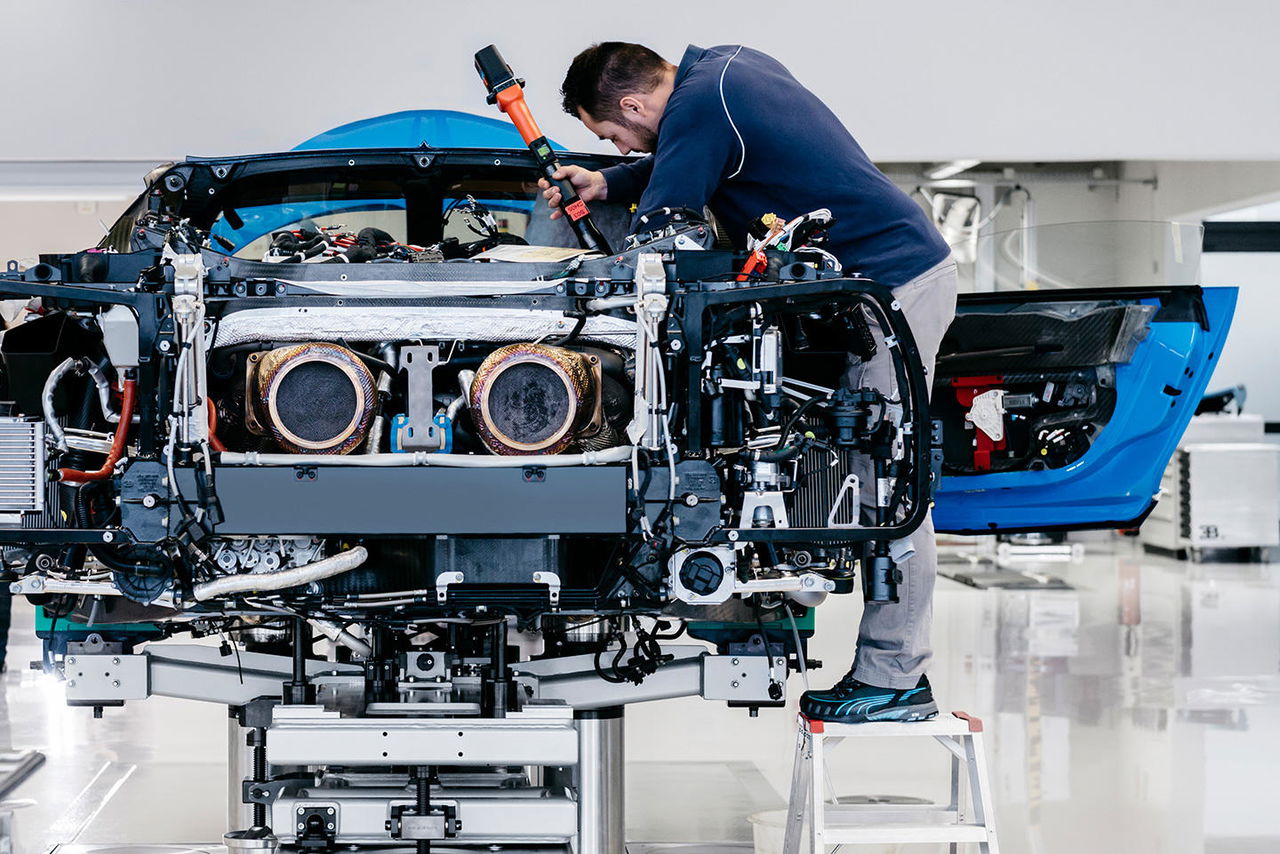
La familia del Bugatti Atelier. 20 empleados, incluidas 2 mujeres, se encargan de todo el proceso de ensamblado, que se dilata en torno a seis meses.
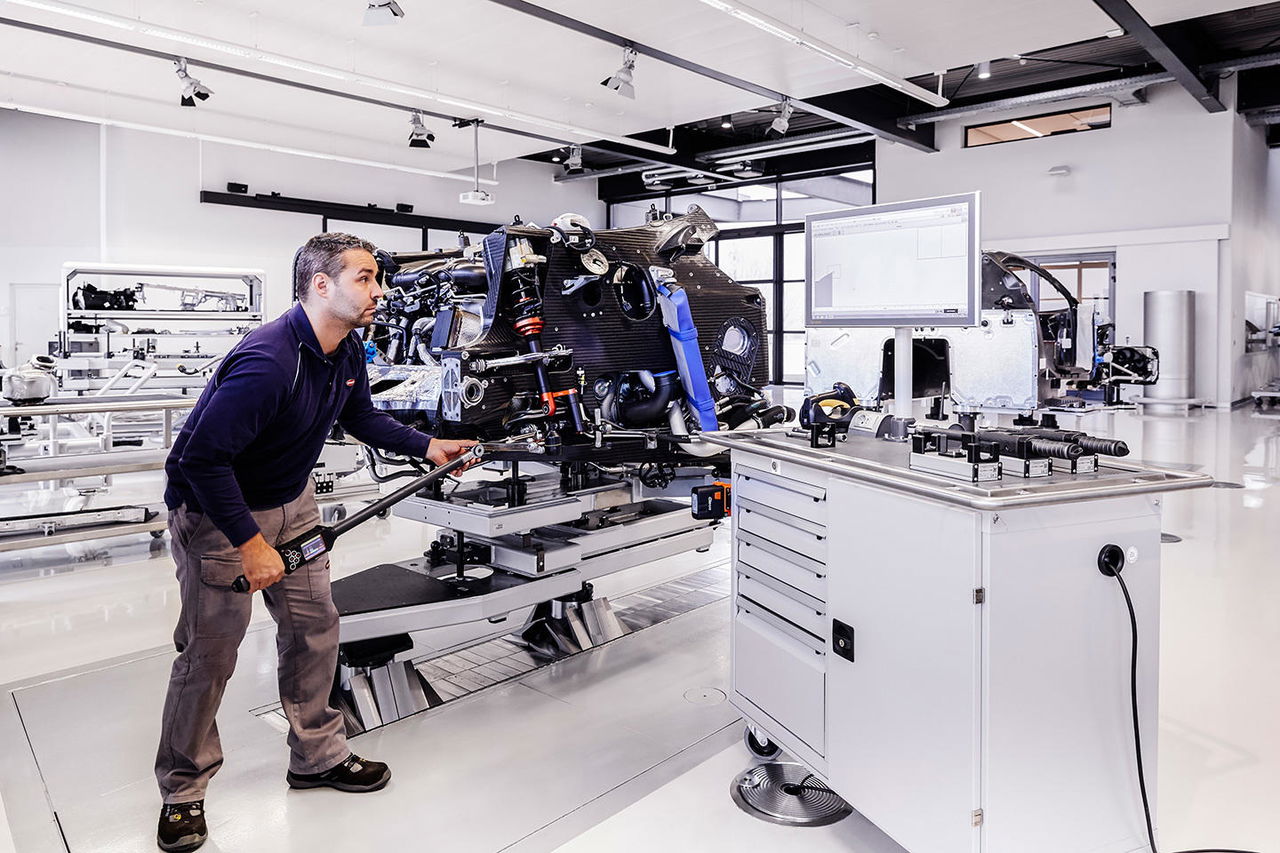
Artesanía y alta tecnología. Tan concienzudo y detallado es el trabajo de ensamblado de un Bugatti Chiron que se registra, incluso, el operario que realizó la operación y el par de apriete empleado para atornillar 1.068 componentes.
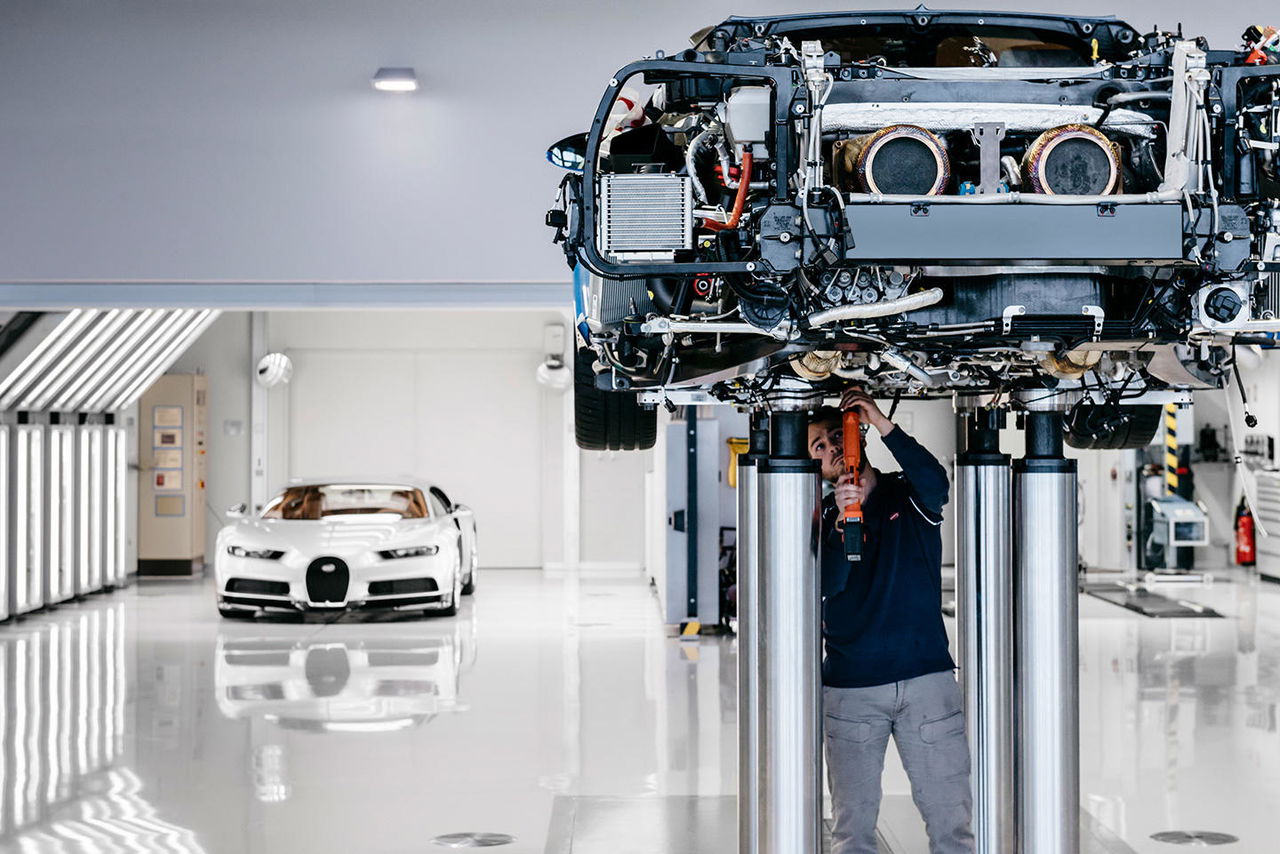
La refrigeración del Bugatti Chiron. Dado que uno de los apartados más importantes del Bugatti Chiron pasa por el trabajo de sus radiadores y la refrigeración del motor, Bugatti llena los circuitos de refrigeración, los drena, y los vuelve a llenar, durante ciclos para asegurarse de que no exista ninguna fuga.
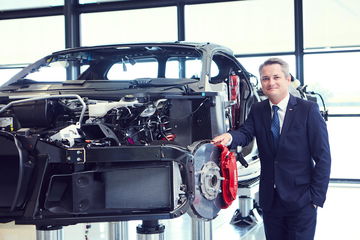
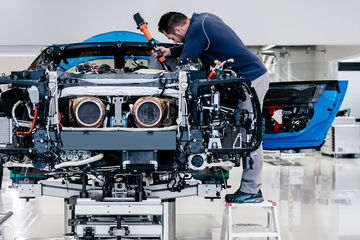
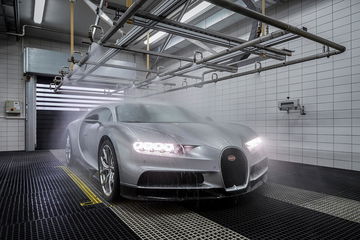
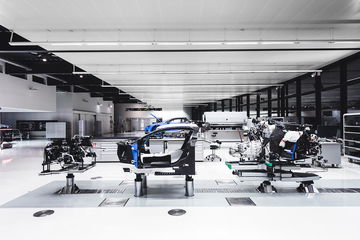
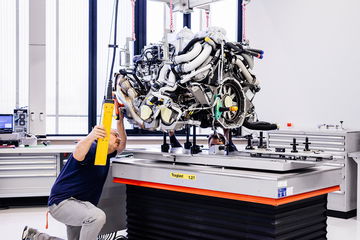
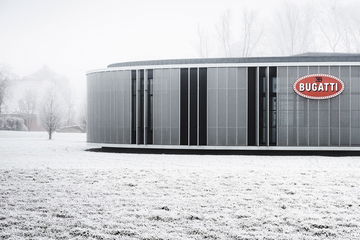
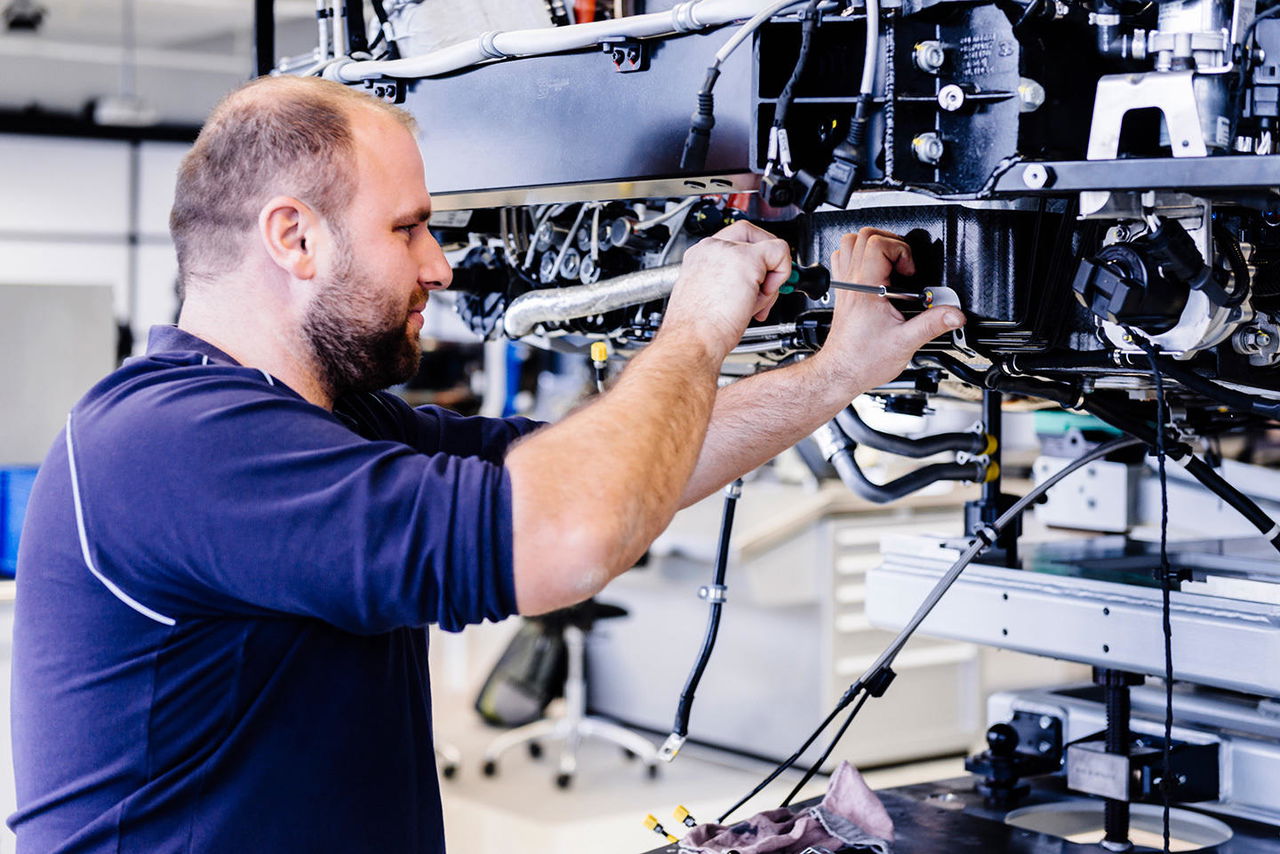
Un enorme LEGO. Cada Bugatti Chiron se compone de un total de 1.800 piezas individuales que han de ensamblarse en Molsheim.
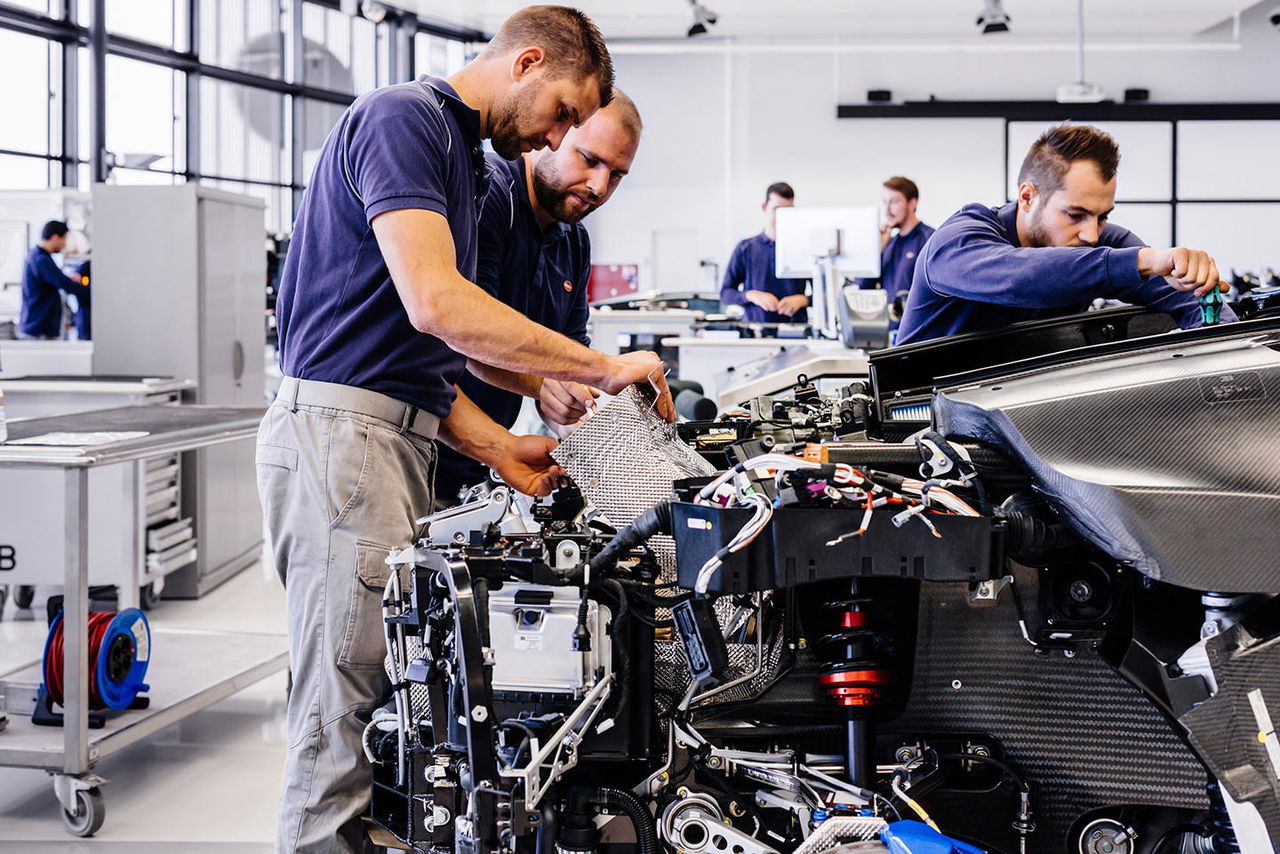
El proceso de calidad. Tan importante como que el ensamblado se lleve a cabo con rigor, y todos los procesos estén bien documentados, el hecho de que cada Bugatti Chiron deba enfrentarse a un concienzudo trabajo de pruebas y análisis de calidad antes de llegar a sus clientes.
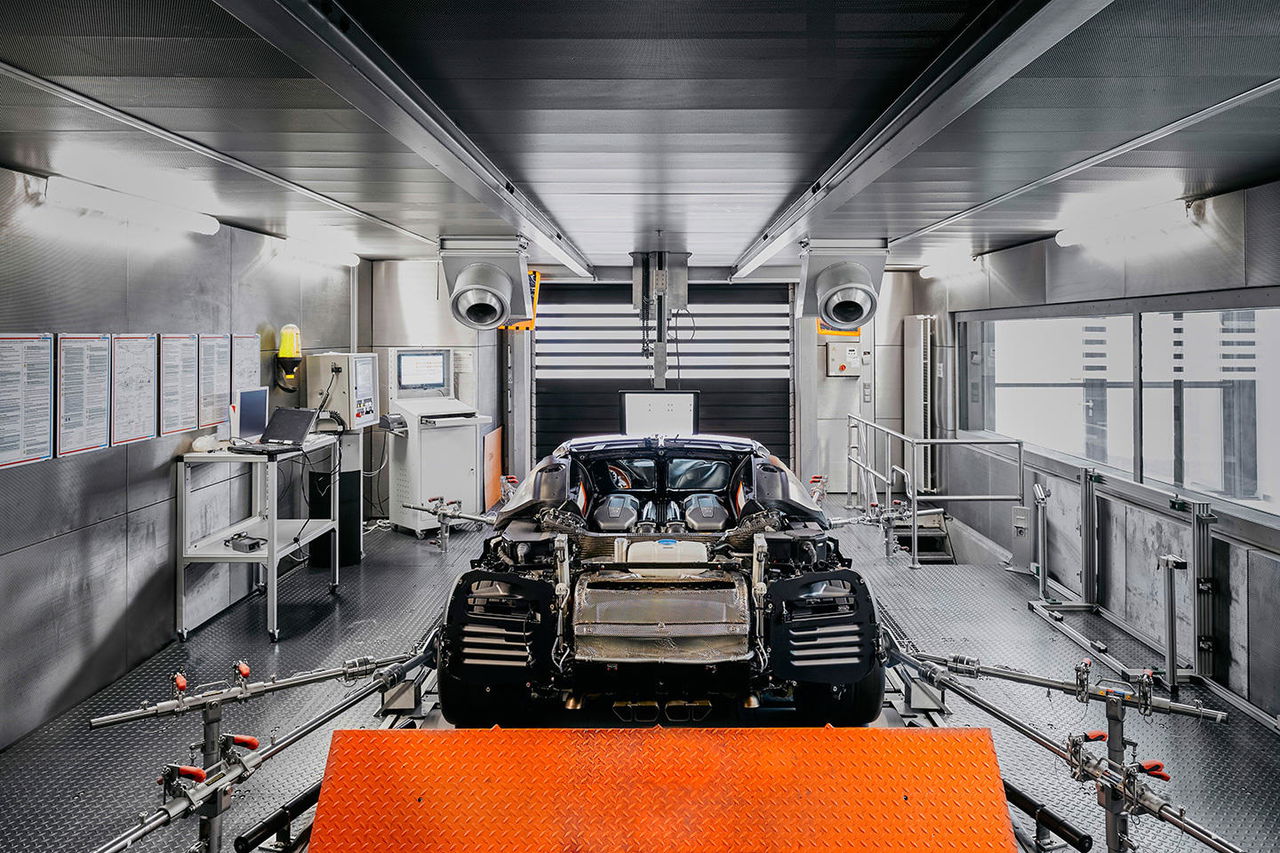
El banco de rodillos de Bugatti. Bugatti trabaja con el que, según la marca, es el banco de rodillos más potente del mundo. Sobre él tiene que poner se a prueba, y a su máximo rendimiento, un Bugatti Chiron de 1.500 CV de potencia y 1.600 Nm d par máximo y alcanzar velocidades superiores a los 200 km/h. Bugatti ha diseñado un sistema propio para anclar las ruedas del Chiron – que obviamente son unas ruedas diseñadas específicamente para estas pruebas y no las definitivas – por razones de seguridad.
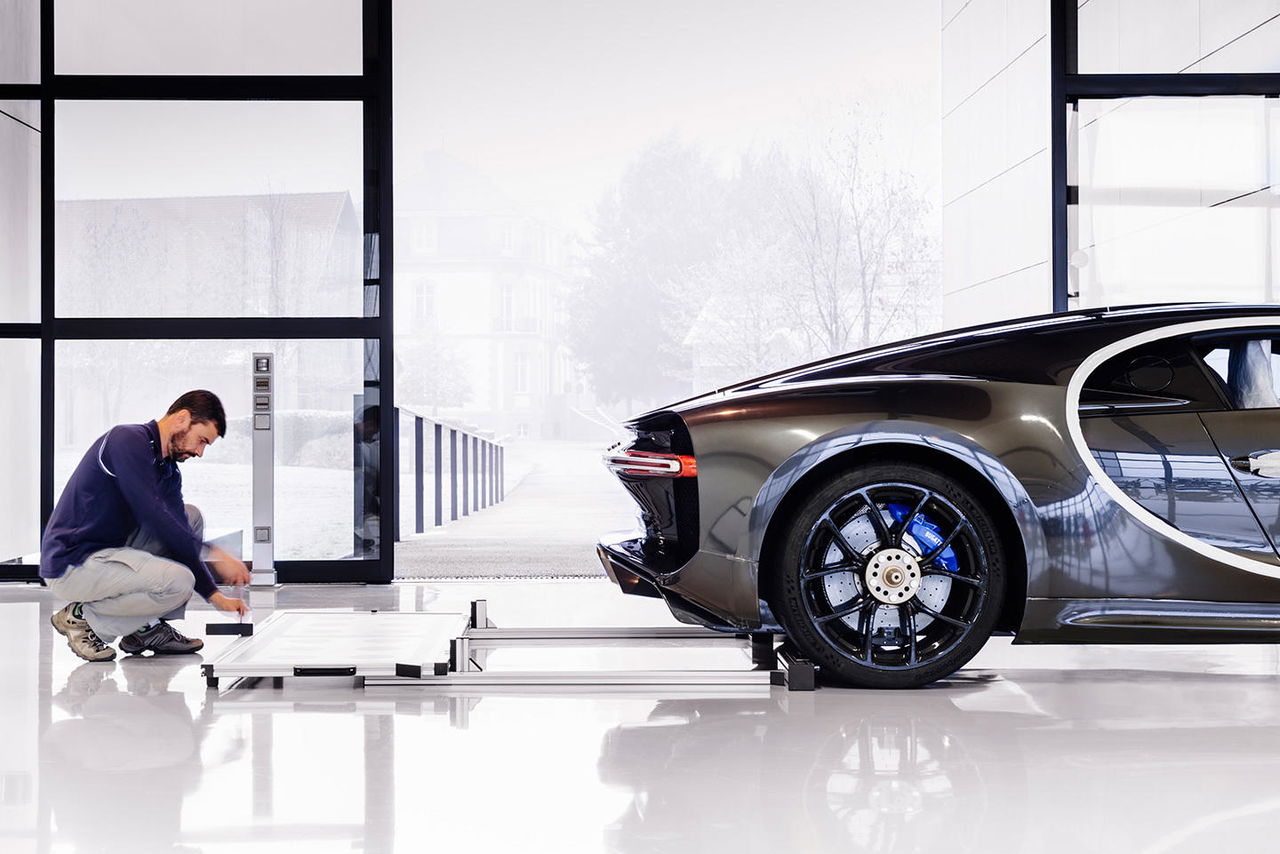
El ensamblado final. El ensamblado final del Bugatti Chiron no termina hasta que cada vehículo pasa por el centro de tecnología de Bugatti, que se encuentra a 200 metros del Atelier. Allí se terminan de ensamblar algunos revestimientos exteriores, muchas piezas más pequeñas y frágiles, que se ensamblan después de las pruebas en el banco de rodillos para evitar cualquier desperfecto.
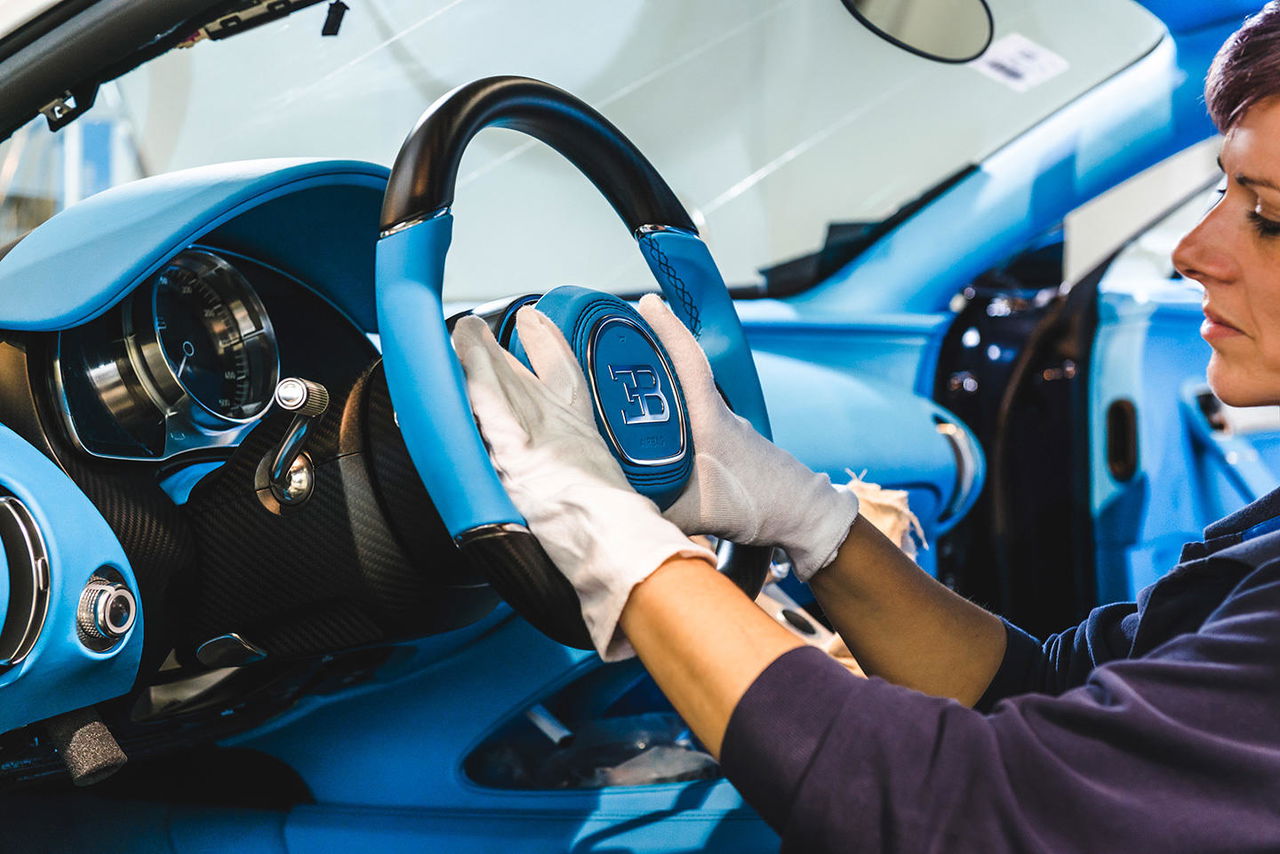
Tratando con mimo hasta el último detalleDecía Bugatti que sus clientes no solo pueden escoger acabados de pintura y tapizados de tela y piel procedentes de una paleta con decenas de colores, sino que también pueden solicitar cualquier personalización que requieran. Personalizaciones típicas, y habituales en sus clientes, como escoger un acabado de pintura exterior a juego con un bolso, o pedir la inscripción de sus iniciales en los reposacabezas y en la base del alerón trasero.
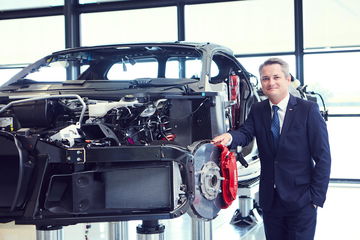
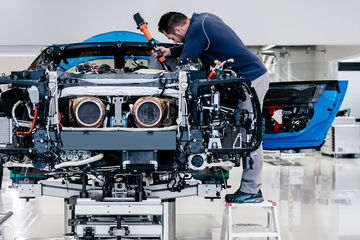
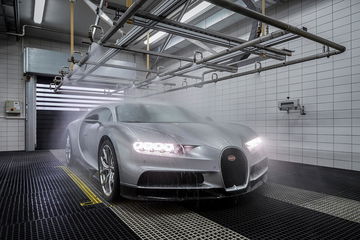
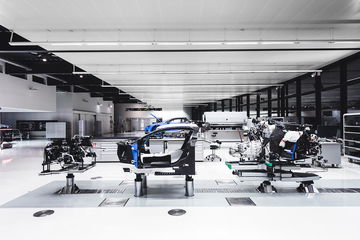
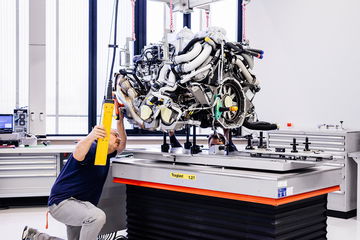
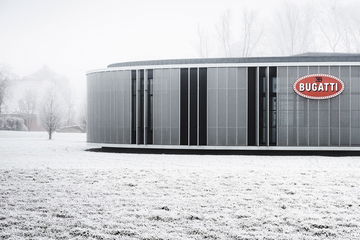
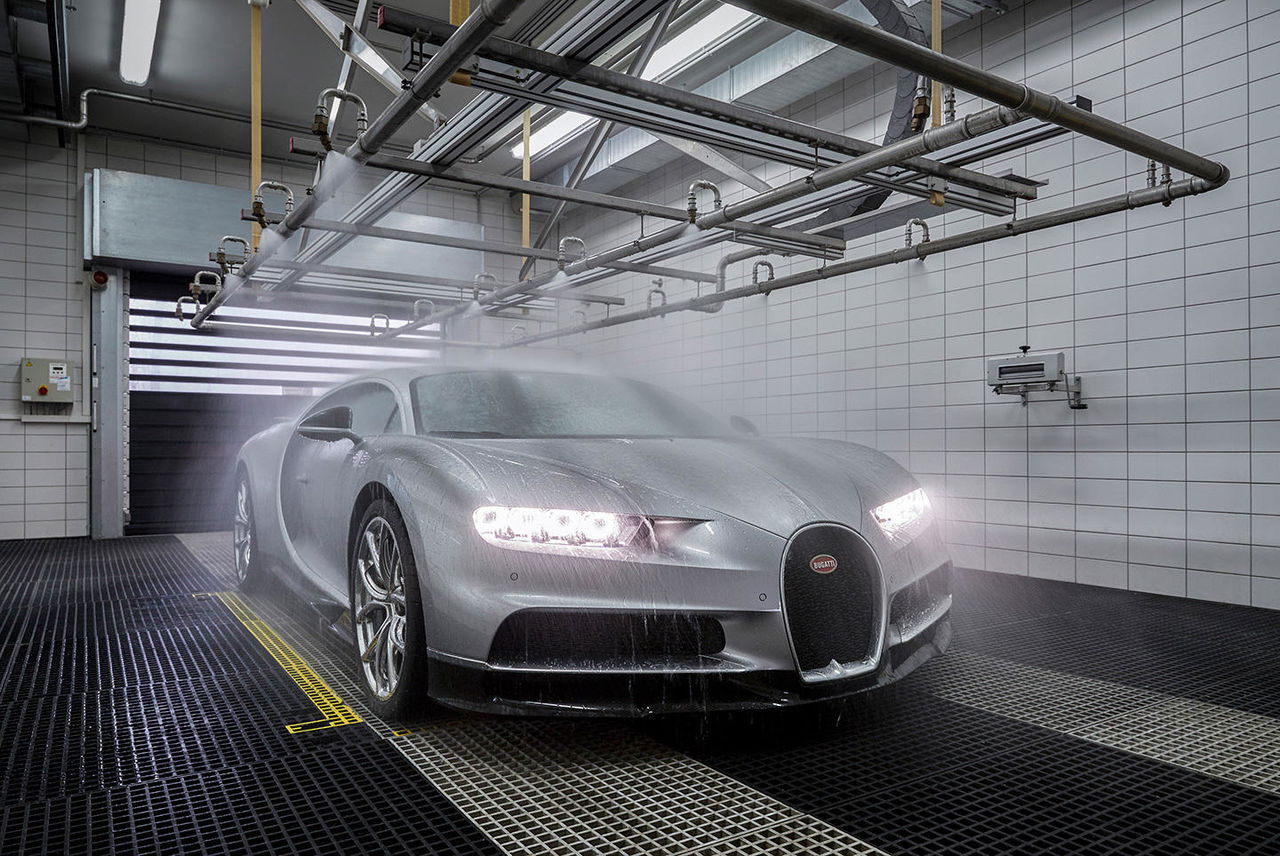
Túnel meteorológico. Cada Bugatti Chiron pasa por un túnel de pruebas en el que Bugatti simula lluvias de diferente intensidad, llegando al aguacero al que se enfrentaría un Bugatti en pleno monzón, durante 30 minutos. En esta etapa se intenta asegurar que el habitáculo del Bugatti Chiron es estanco, incluso en las peores condiciones.
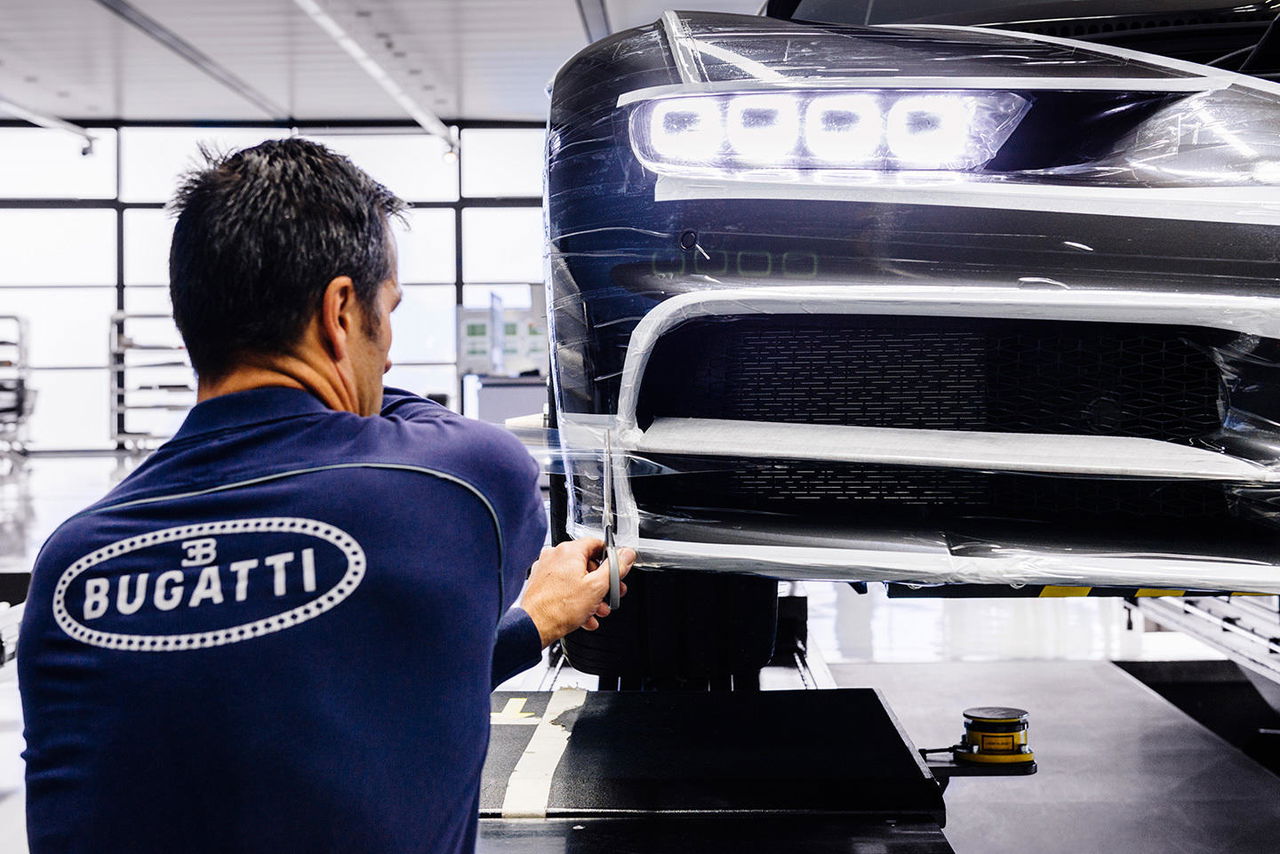
El proceso de pinturaBugatti dedica en torno a tres semanas únicamente al proceso de pintura de cada Bugatti Chiron.
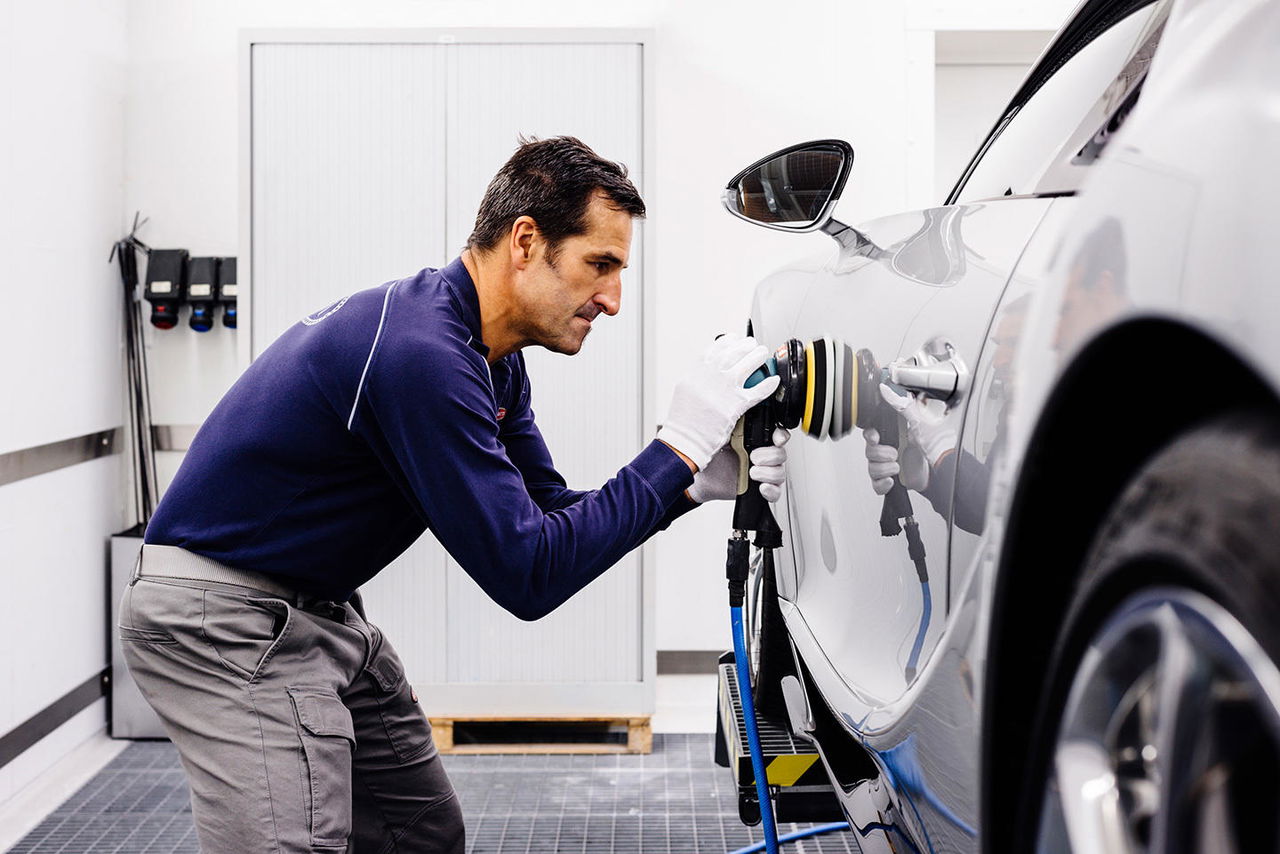
Los acabados de pintura más sofisticados del mundo. Según el acabado escogido, se pueden llegar a aplicar entre seis y ocho capas de pintura, en un proceso completamente manual, que requiere la aplicación de cada capa y un cuidadoso proceso de pulimento.
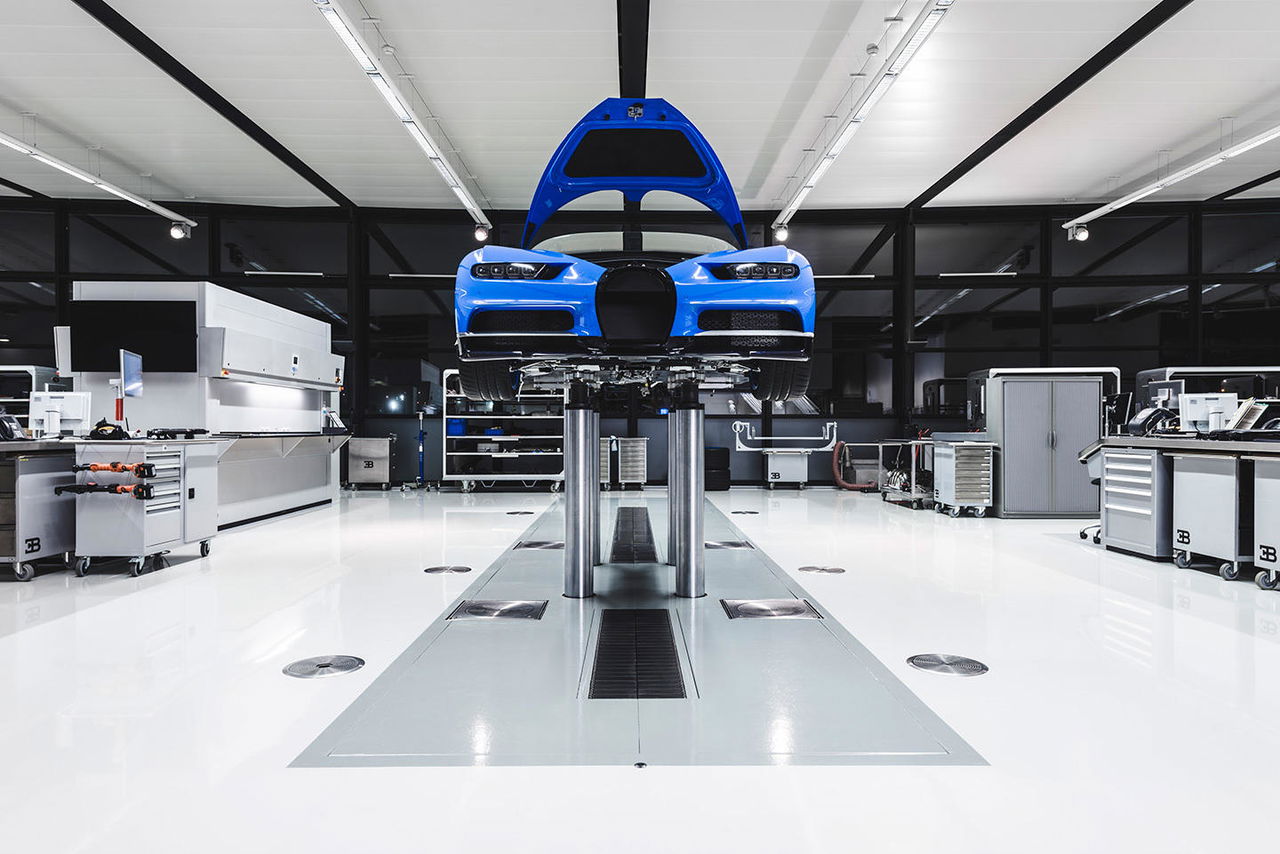
Más de 70 coches al año. Con un proceso de ensamblado tan laborioso y detallado, sorprende que según Bugatti vayan a ensamblarse un total de 70 unidades del Bugatti Chiron a lo largo de este año. Cifras ridículas si las comparamos con las de cualquier otra fábrica de coches, donde la producción se mide en decenas y cientos de miles de unidades.
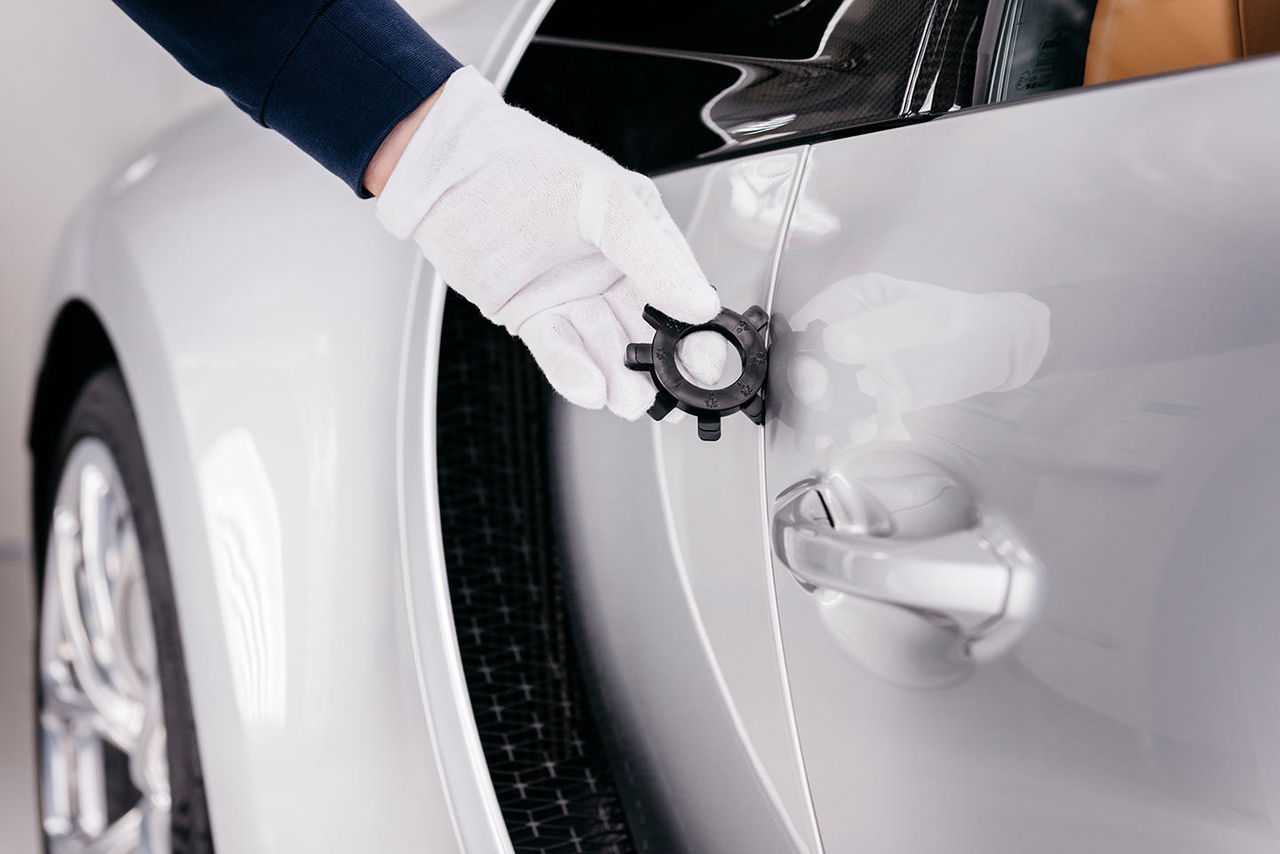
Los procesos de calidad más exhaustivosBugatti asegura que un responsable de calidad inspecciona durante seis horas cada coche, identificando cualquier desperfecto o aspecto mejorable. En algunos casos ese proceso puede alargarse más de tres semanas, si se requiere volver a instalar un componente muy personalizado que necesita ser fabricado de nuevo.
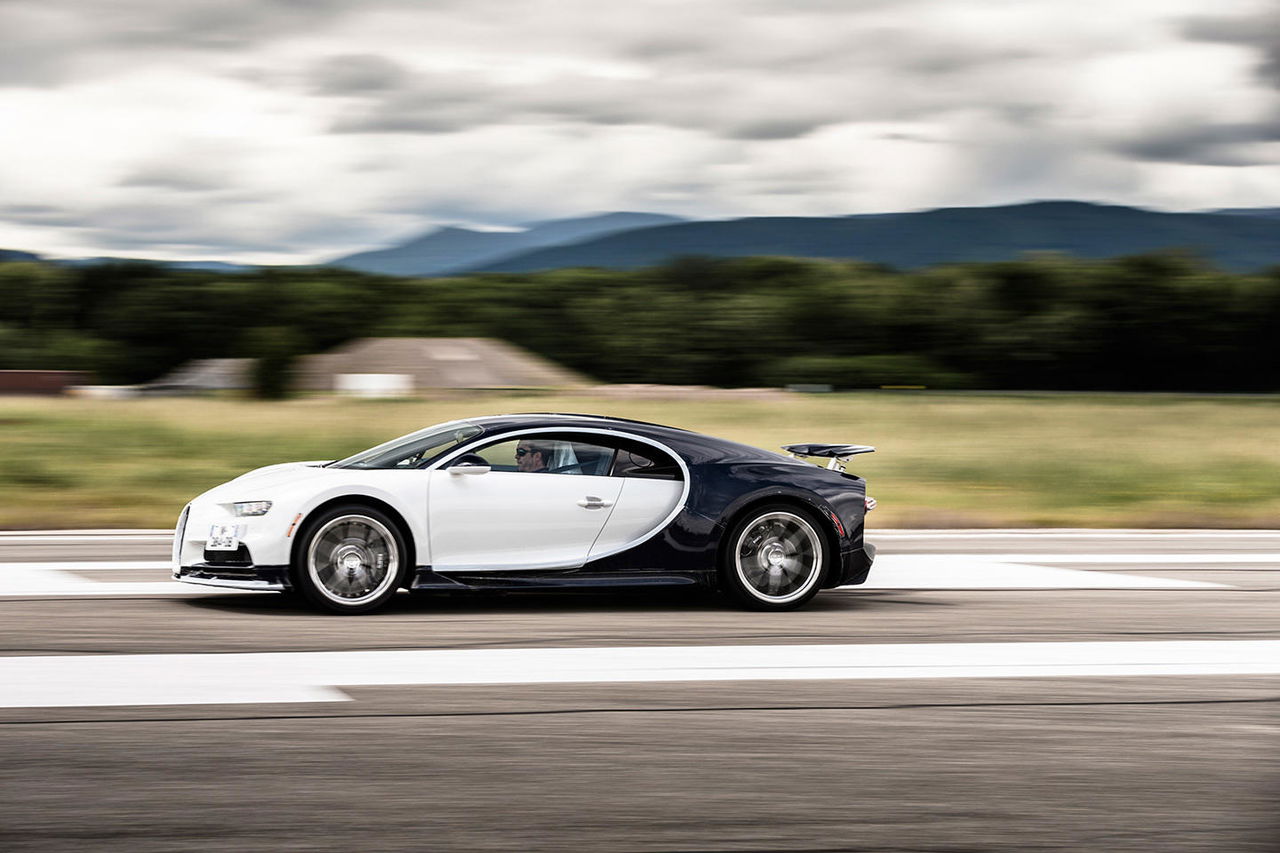
A 250 km/h por la Autobahn. Antes de su entrega, Bugatti se asegura de que el Chiron está en perfectas condiciones con una prueba, en pista cerrada, y Autobahn, en la que se llegan a alcanzar velocidades superiores a 250 km/h. Tras la prueba, Bugatti remplaza el suelo plano del coche y las llantas – para evitar desperfectos – e incluso realiza un cambio del aceite de la transmisión.
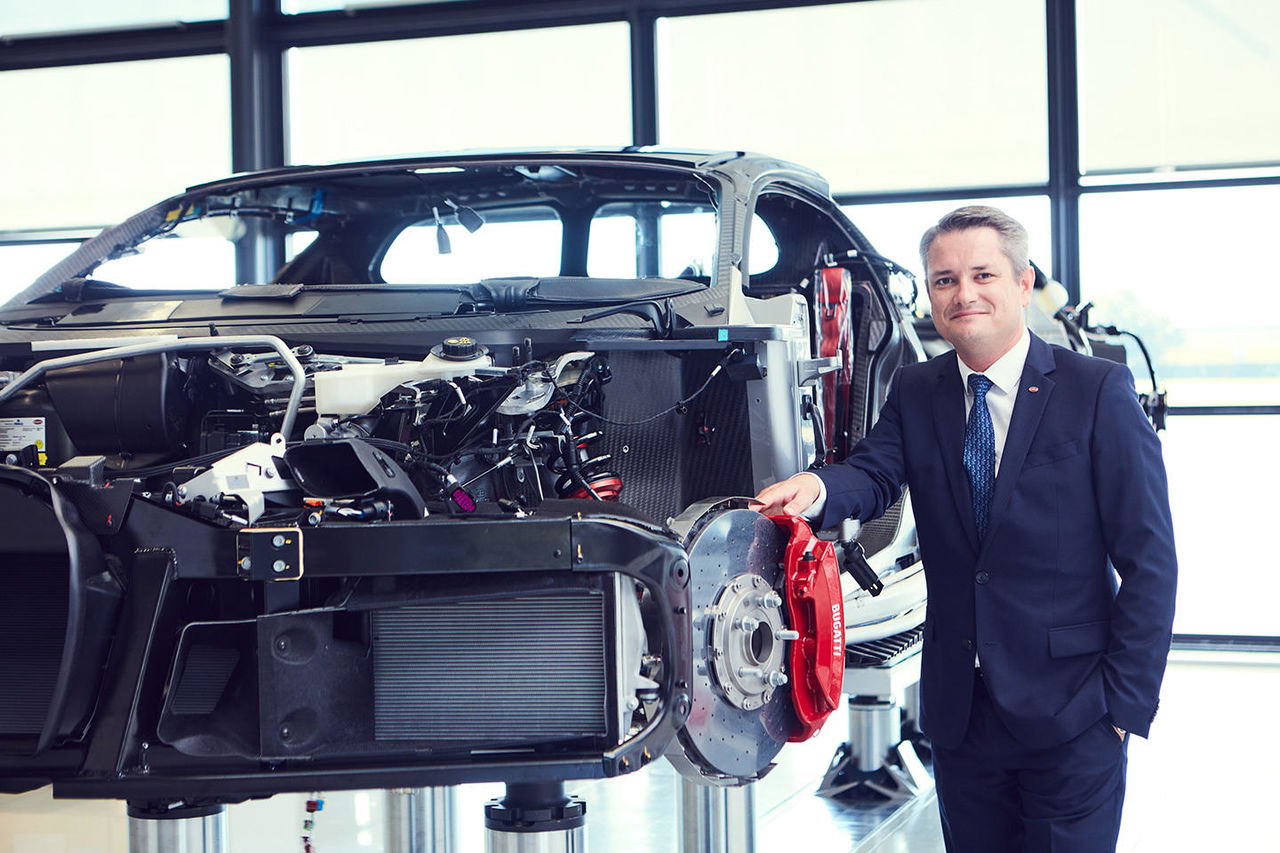
Flying Doctors. Tras el proceso de fabricación, la responsabilidad del buen estado de cada Bugatti Chiron que exista en el mundo recaerá en los Flying Doctors. Estos «doctores voladores», según la traducción literal, son mecánicos capaces de desplazarse en unas horas a cualquier parte del mundo para reparar un Bugatti Chiron que lo necesite.
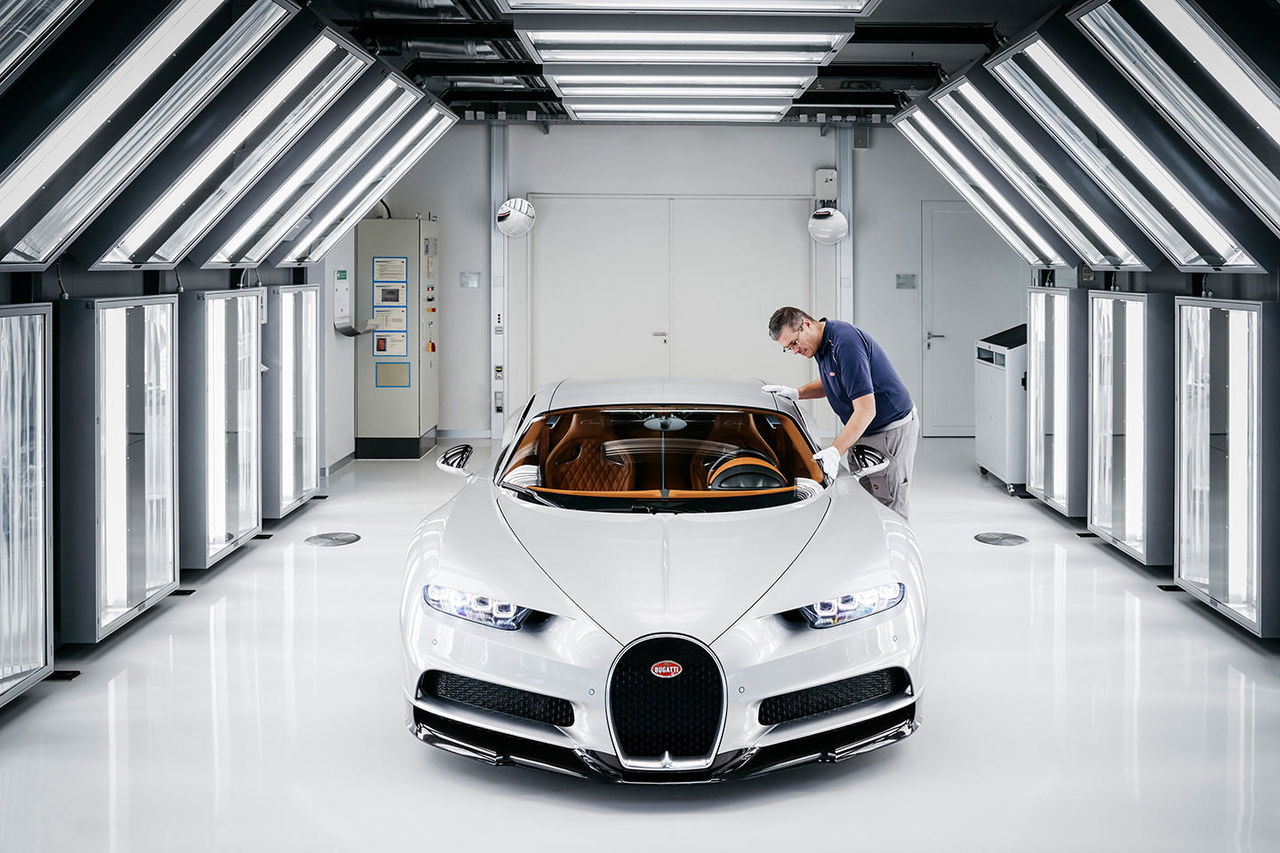
Listo para su entrega. Ningún Bugatti Chiron sale de Molsheim sin que antes lo hayan aprobado todos los responsables de calidad de la fábrica. No se deja nada al azar.
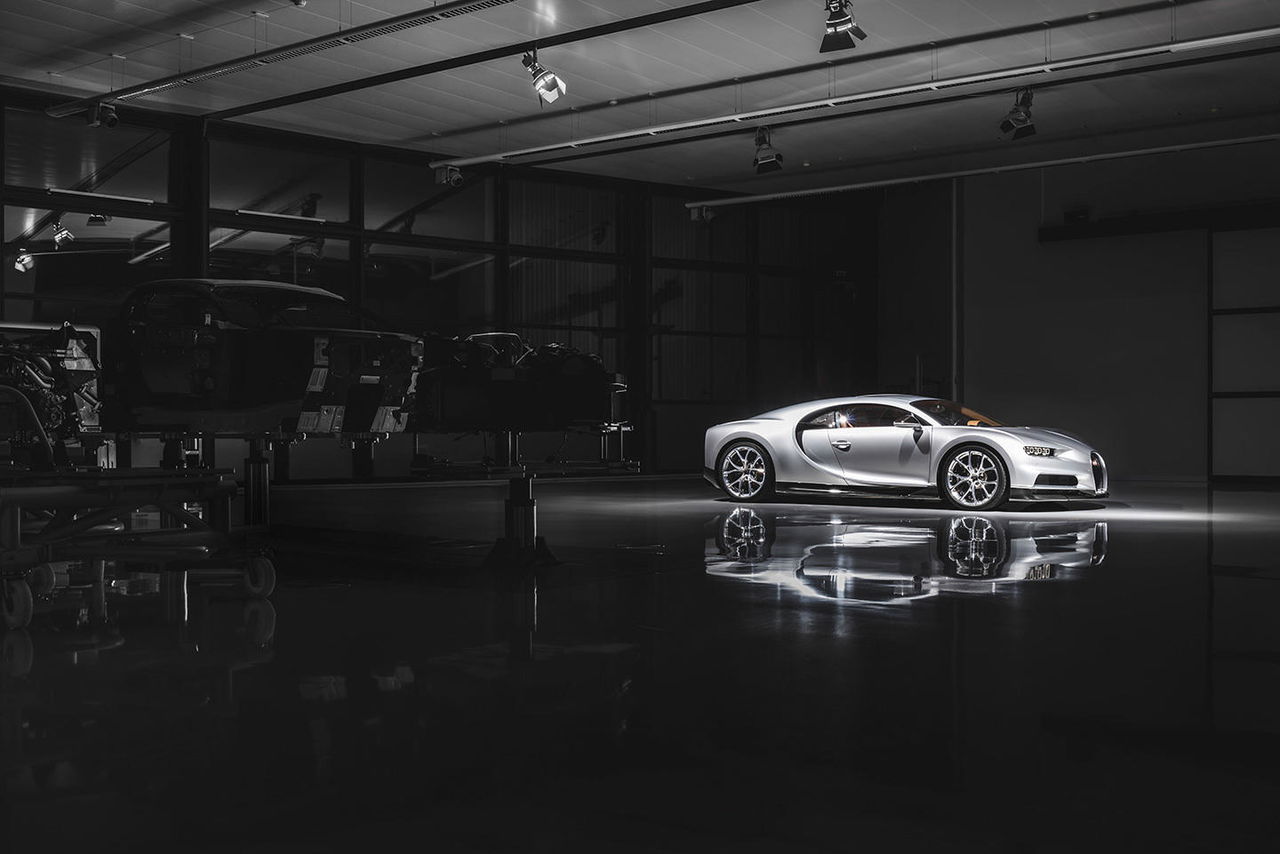
La entrega. Y si todo ha ido bien. El cliente recibirá su Bugatti Chiron en un tiempo aproximado de nueve meses desde que cerró su configurador con el diseñador de la marca.
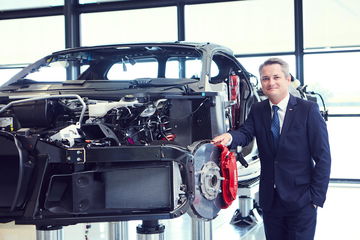
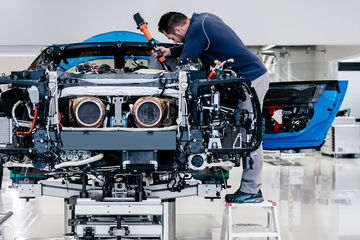
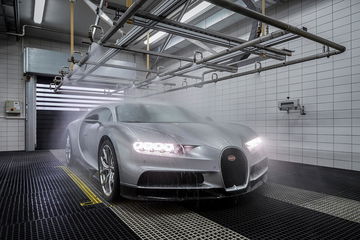
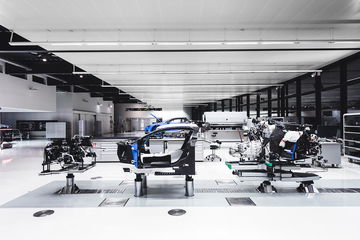
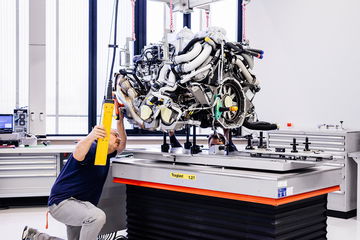
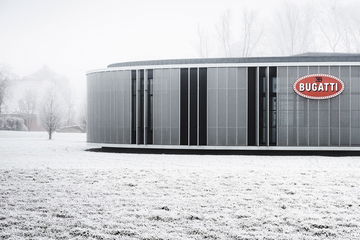